Complete Production and Process Monitoring Capabilities
SYSCON PlantStar provides Manufacturing Execution Systems (MES) solutions that collect Production and Process data for use by manufacturing, quality control, management, accounting and financial systems. Traditionally Manufacturing Execution Systems provide users and management teams with key information about the manufacturing process as well as the Overall Equipment Efficiency (OEE) of the equipment being monitored.
When you need to know everything that’s happening with your production activities and process variables, you need an MES system that delivers the right functionality. From drag-and-drop job scheduling to real-time dashboard reporting and customizable alerts, PlantStar's manufacturing execution system is designed to help you do what you do best. With a full range of capabilities and continuous updates, PlantStar's MES software has the solutions you and your company need to maximize overall equipment effectiveness (OEE). It’s time to reach your full potential.
Production Monitoring Features
Production Monitoring involves counting the rate that parts are being reduced.
Get insight into job-specific details on every machine so you can keep track of upcoming projects, potential downtime, reducing scrap and create your customized reports in real-time. PlantStar's MES features puts you in control by allowing you to customize your MES system.
Job Scheduler
Job Summary
Job Shift Summary
Production Summary
Job Setup Sheets
Customizable Charts and Reporting
Real-Time Dashboards
Downtime and Scrap Reporting
Instant Alerts
Defect Collection
Labor Tracking
Material and Tool Tracking
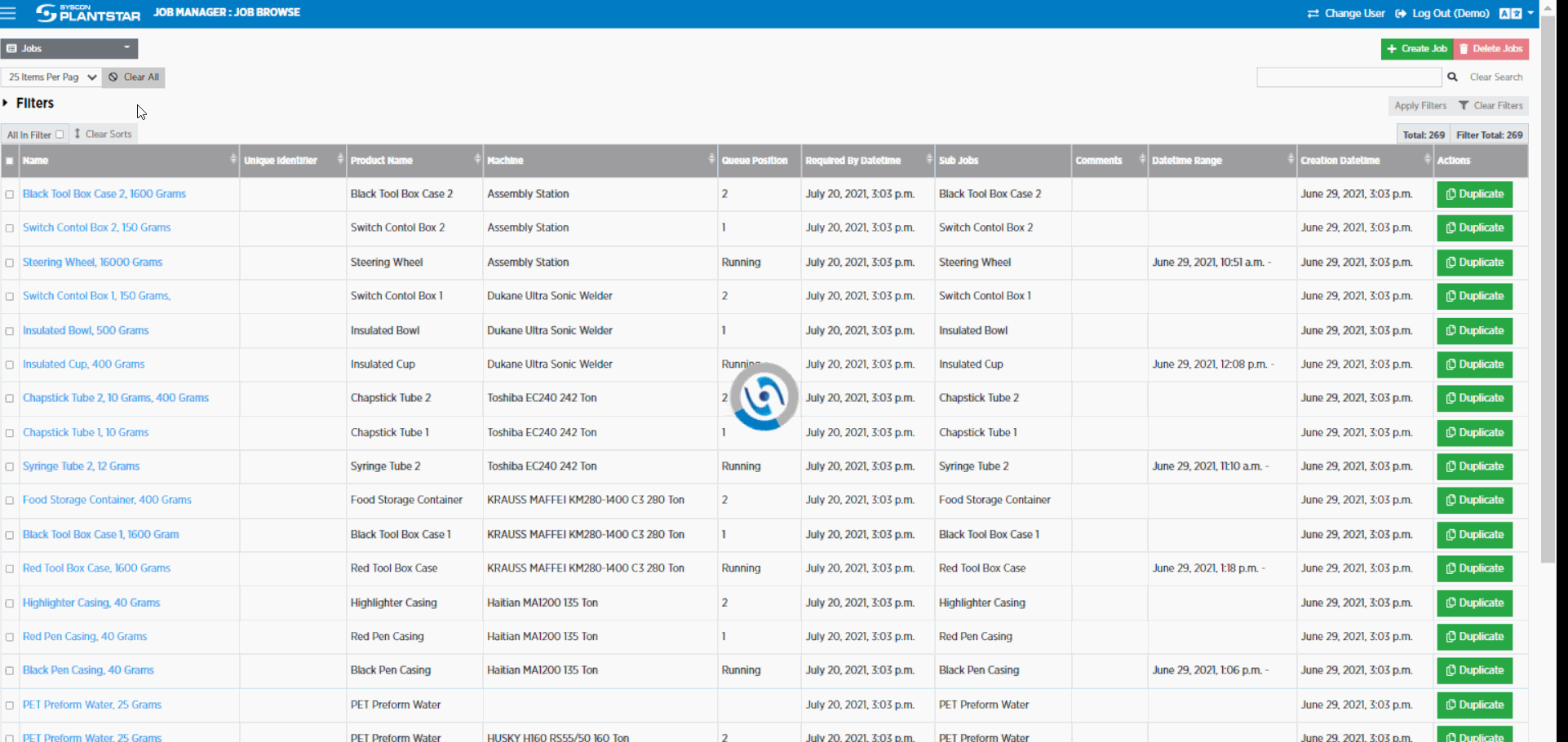
to Enlarge
Job Scheduler
Simplify job scheduling with a drag-and-drop tool that makes it easy to move projects. The MES shows the current time and tools being used for specific projects, and allows you to update the tools and resources or switch the order of projects in order to avoid collisions.
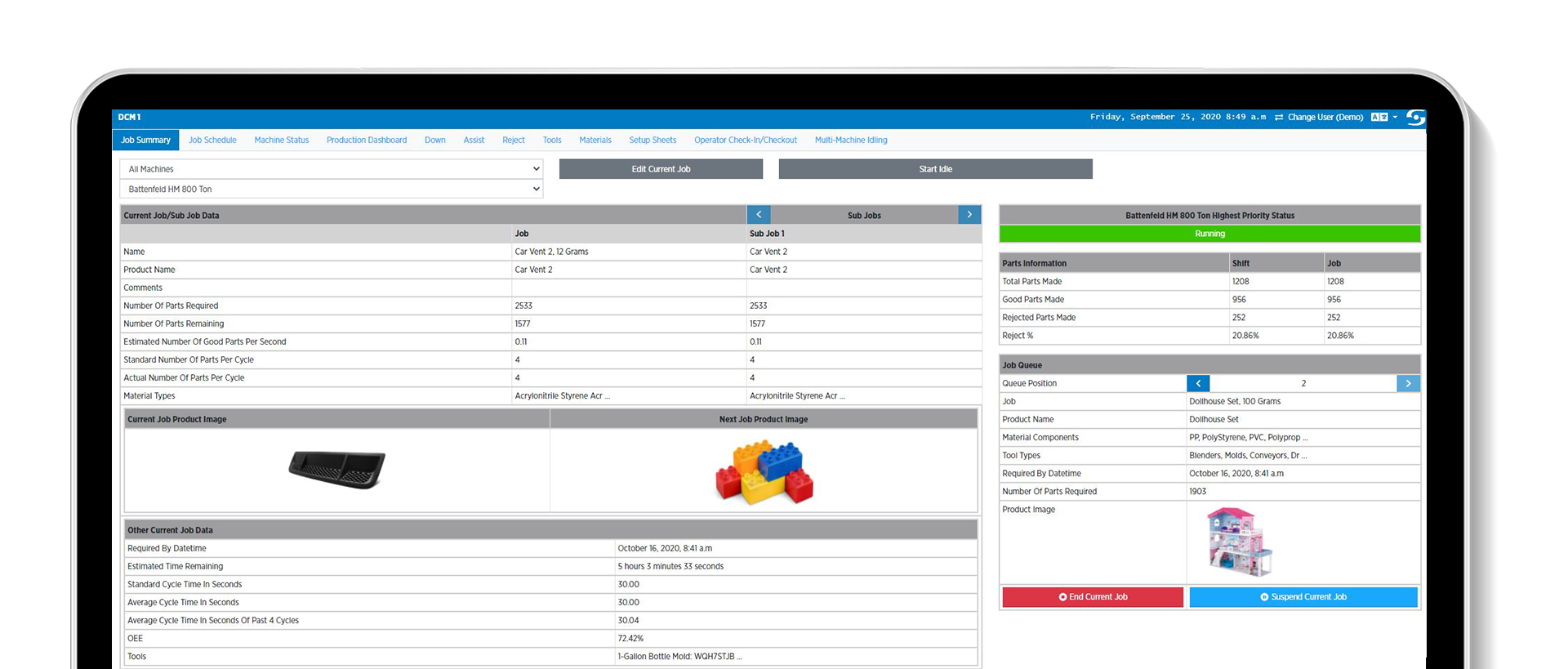
to Enlarge
Job Summary
The job summary screen gives you a quick, up-to-date picture of what is happening on any machine, even those that are not connected to this DCM. With the easy-to-use drop-down menu, you can quickly access important information on a desired machine and make changes to current and future jobs with a touch of the screen.
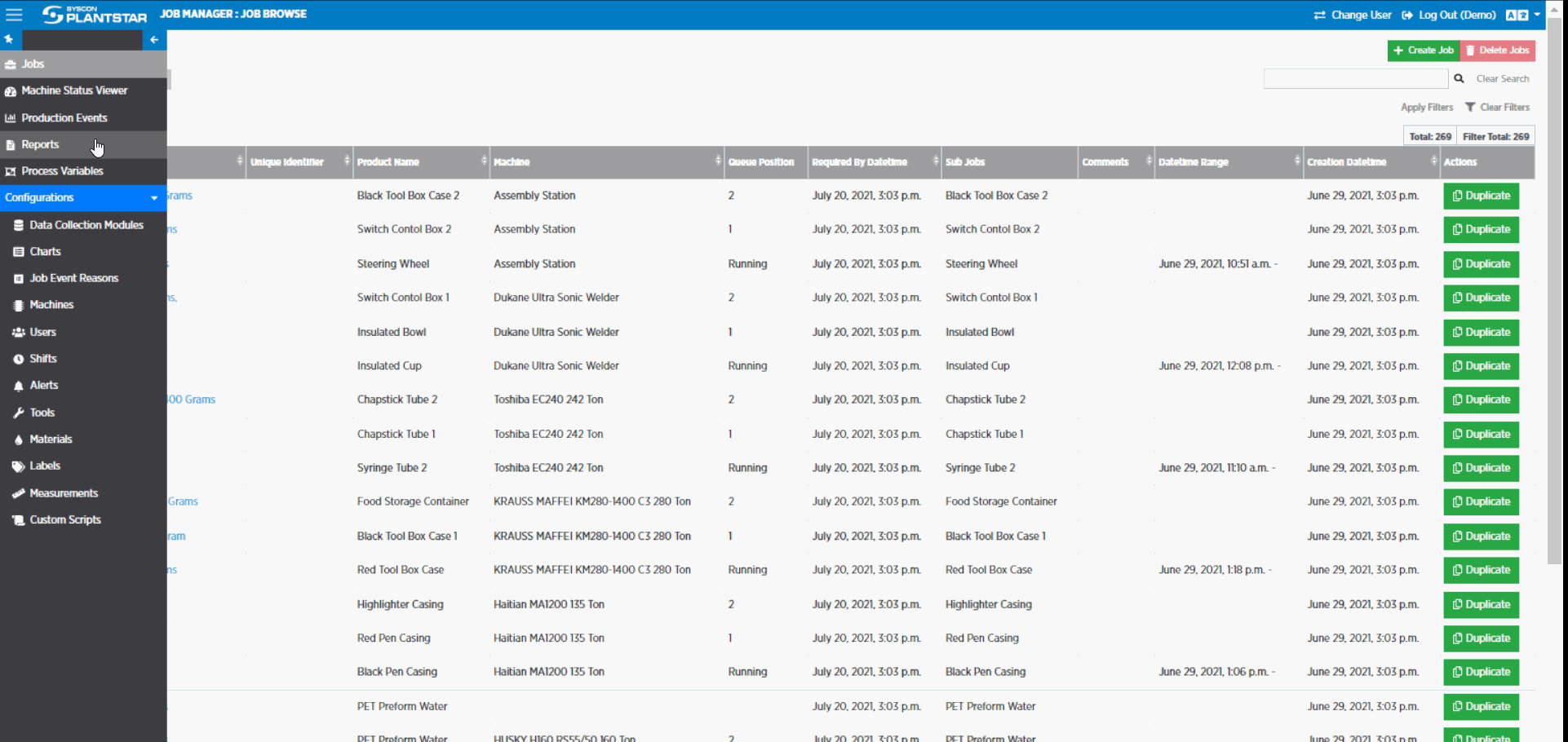
to Enlarge
Job Shift Summary
The Job Shift summary shift by shift data for a particular job
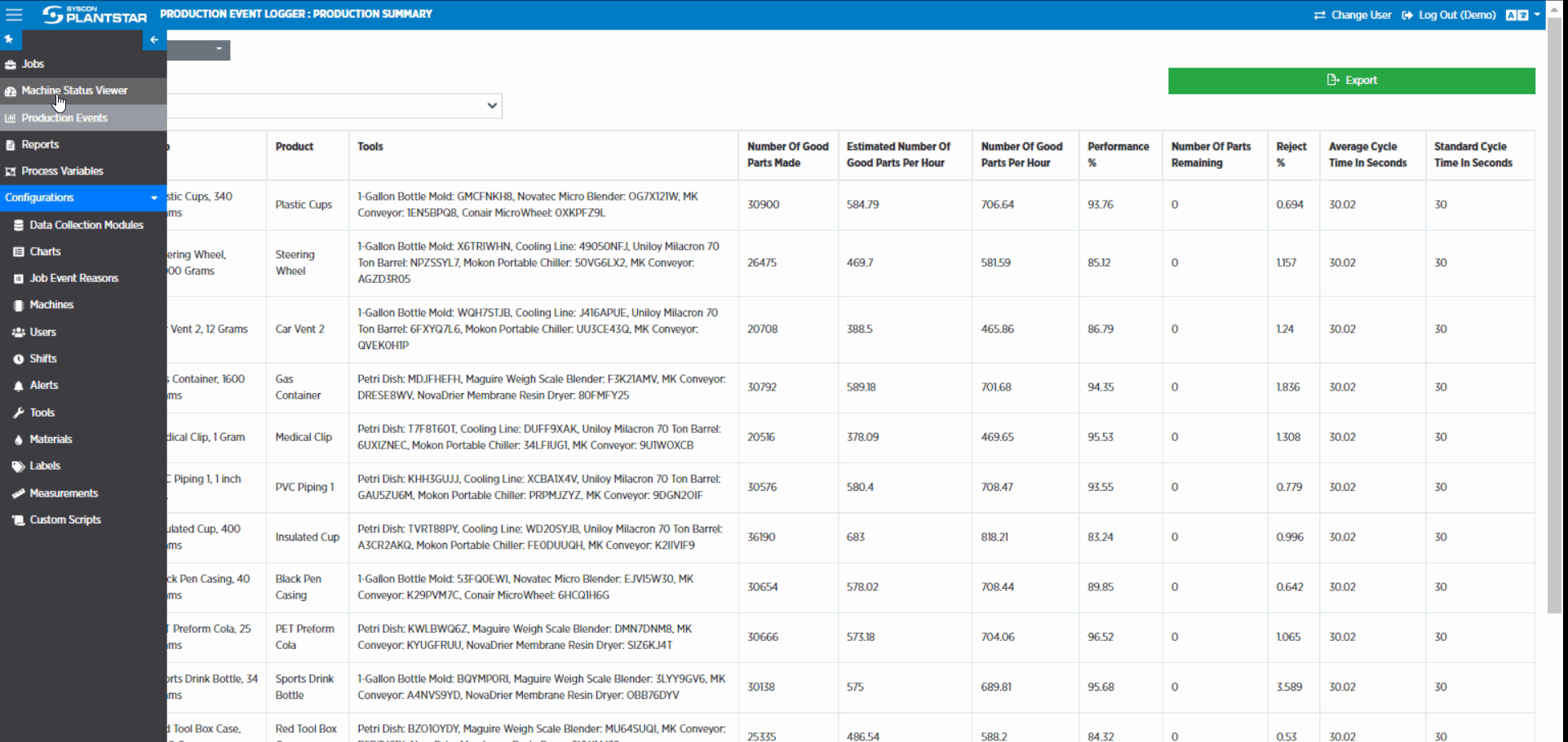
to Enlarge
Production Summary
Real-time production summary events.
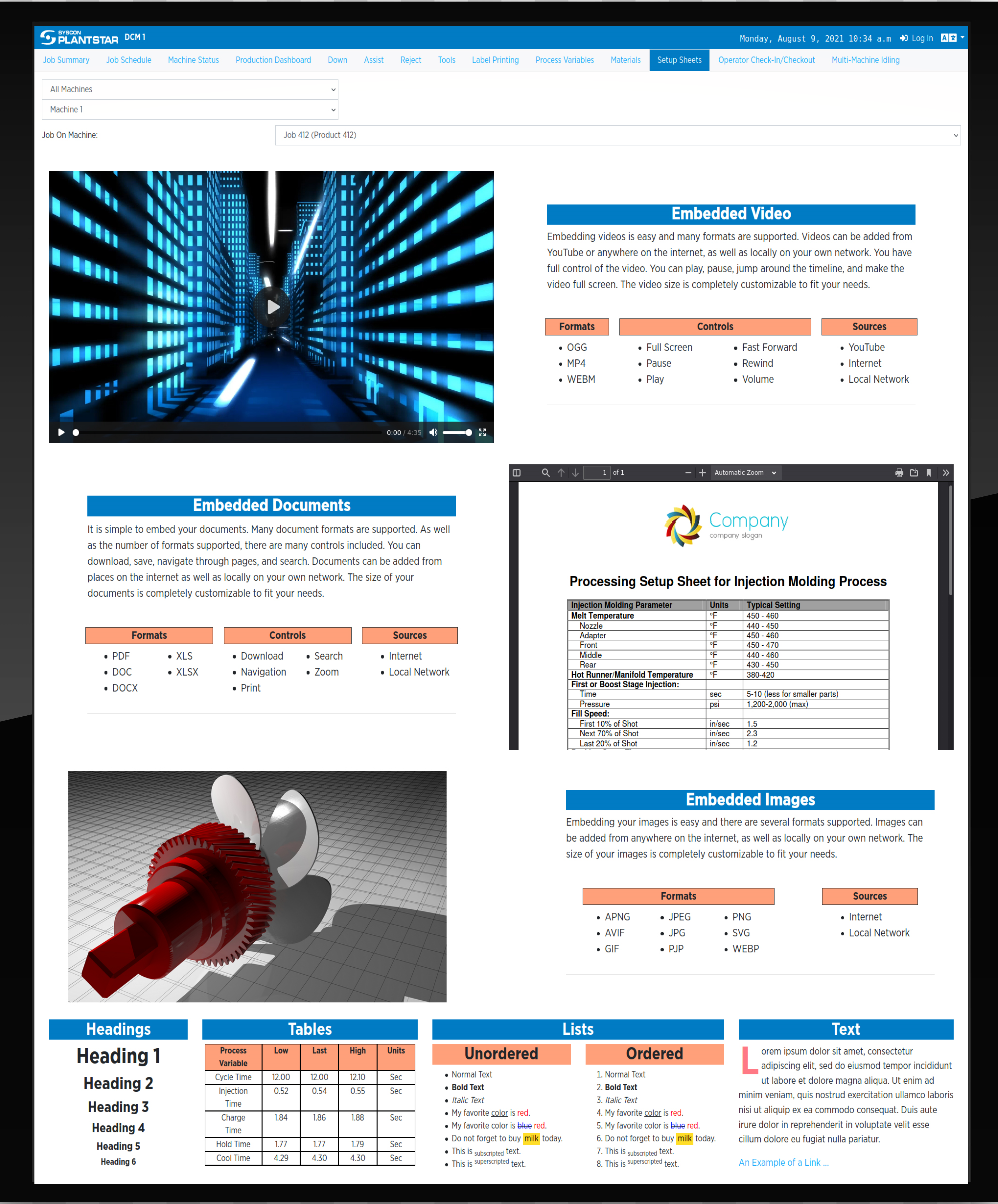
to Enlarge
Job Setup Sheets
Easily access machine setup and miscellaneous summary information. Setup sheets can include training videos, documents, part images, and more.
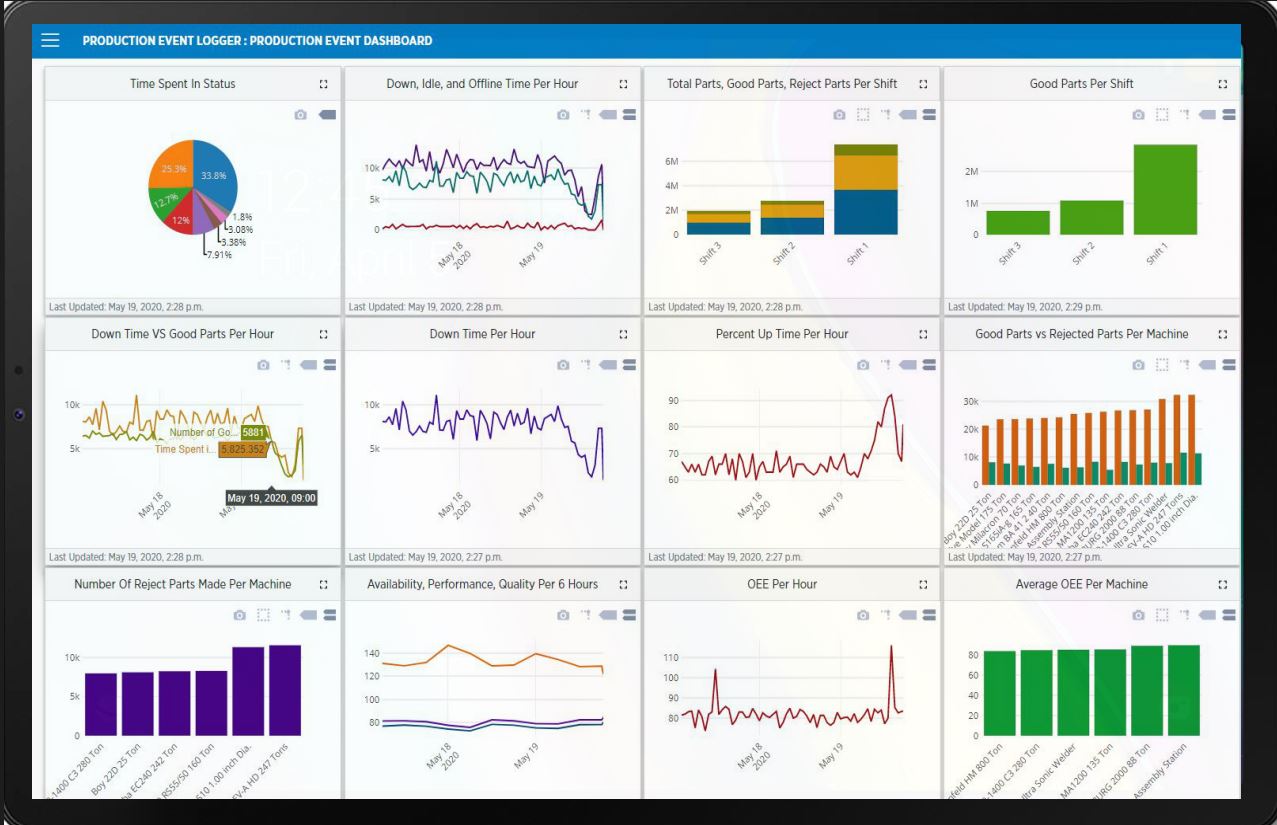
to Enlarge
Customizable Charts and Reporting
Eliminate guesswork as you drive change and implement best practices as a result of data at your fingertips. PlantStar lets you create charts based on your own reporting in real time and auto-schedule report delivery directly to email inboxes, printer, or network folders.
- Prints custom reports
- Schedules custom reports
- Prints scheduled reports automatically
- Reports can be scheduled to print at a specific time
- Reports can be scheduled on a daily basis
- Reports can be scheduled on a weekly basis
- Reports can be scheduled to print at the end of a shift
- Reports can be scheduled to print at the end of each job
- Reports can be printed on any network printer or sent to an HTML file.
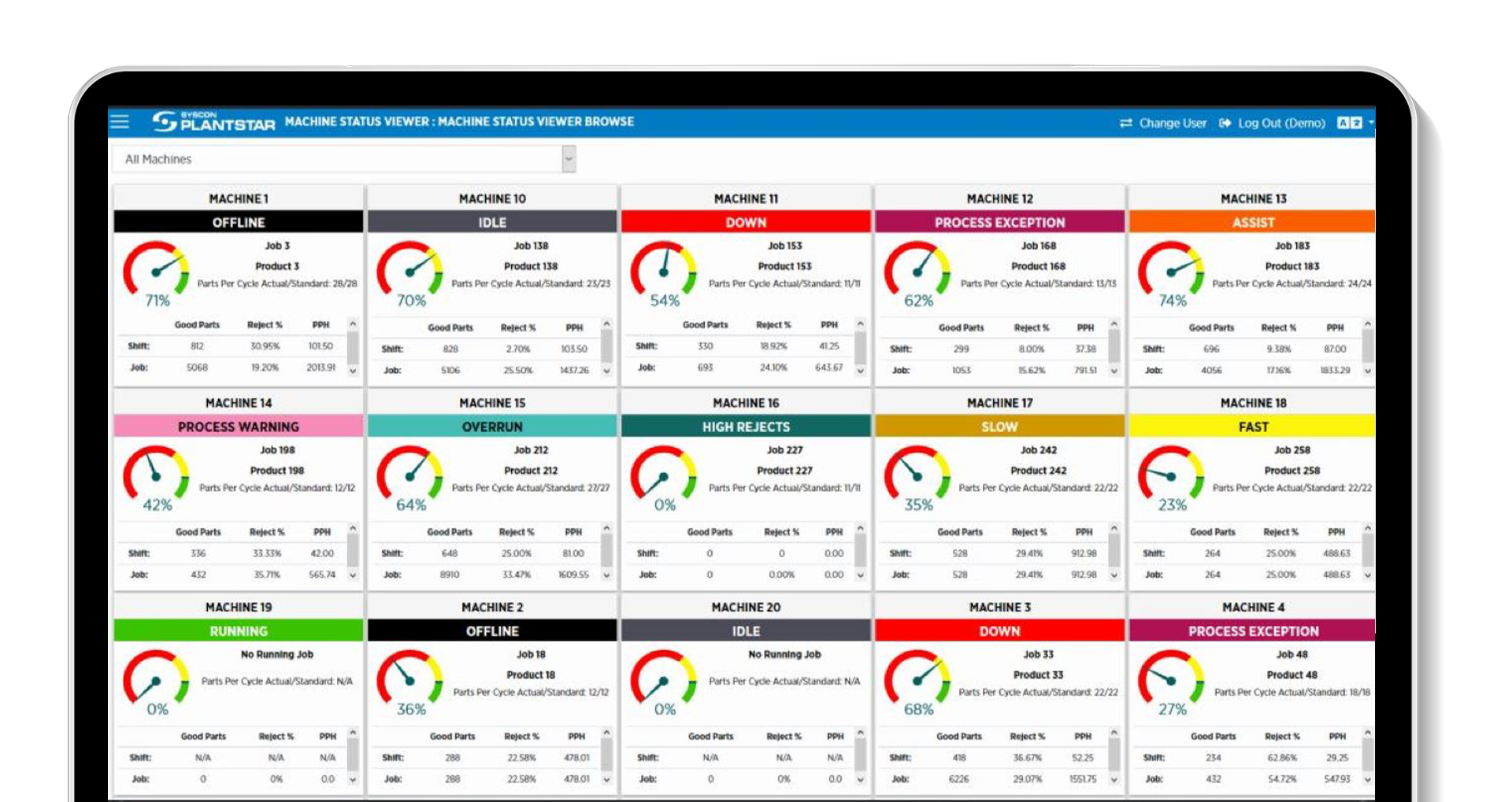
to Enlarge
Real-Time Dashboards
A web based system allows you to view real time charts, reports, and all machine status from any device. Large Screens are used throughout the facility to show data in real-time.
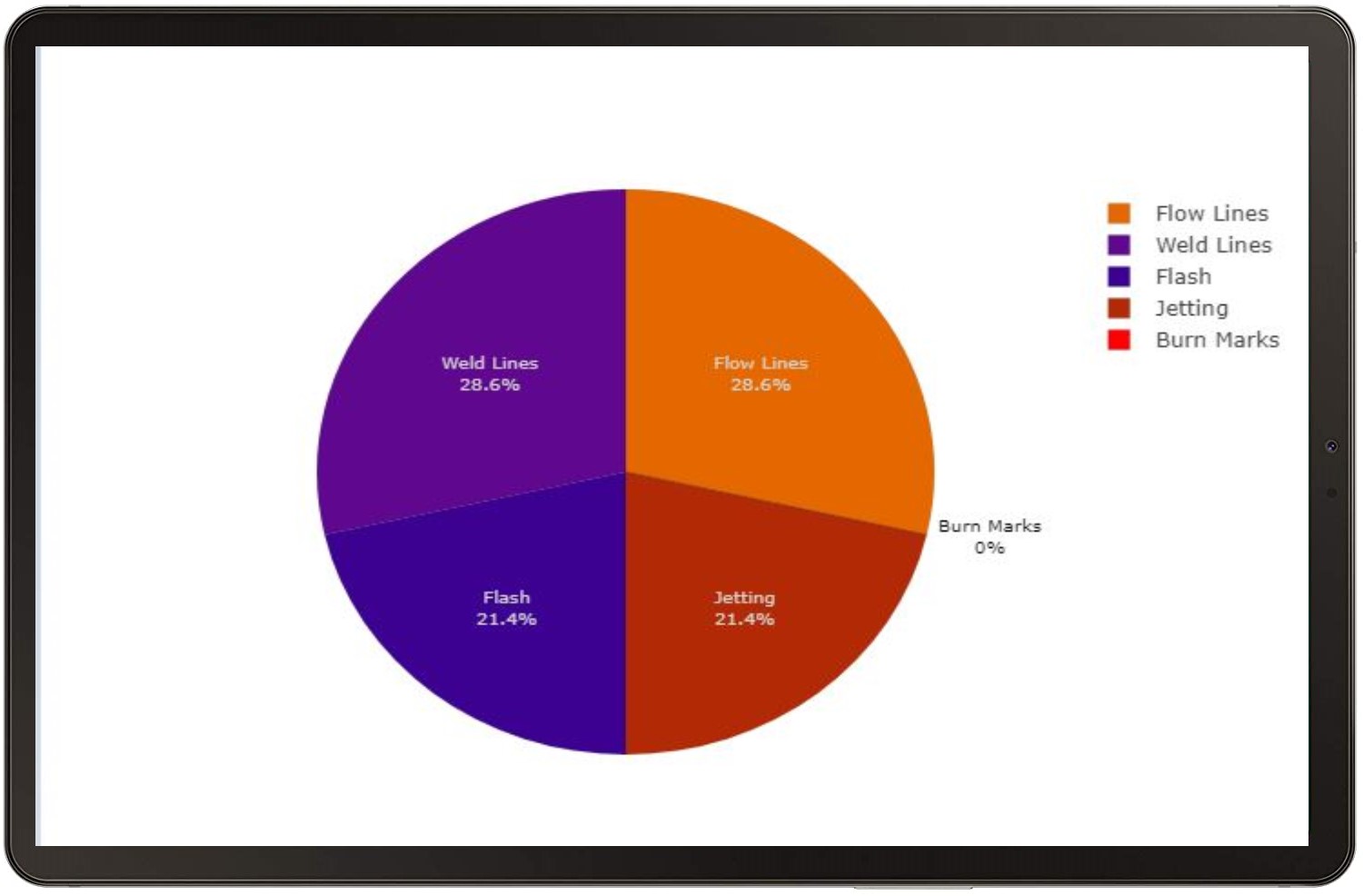
to Enlarge
Downtime and Scrap Reporting
Get alerts when your machines go down and maintain a record of each occurrence. The system tracks the top causes of downtime for each machine and displays the percentage of time taken up by each down. PlantStar 4.0 comes with unlimited down, reject, assist reasons.

to Enlarge
Instant Alerts
The PlantStar 4.0 systems comes with email and text alerts. There is also the ability to add voice (PA Alerts).
Proper personnel can receive an instant alert. Some of the Alert examples are: Process Alerts, high rejects/scrap, downtime, idle status, etc. Now you can react immediately by receving real-time alerts to proactively improve your overall manufacturing goals.
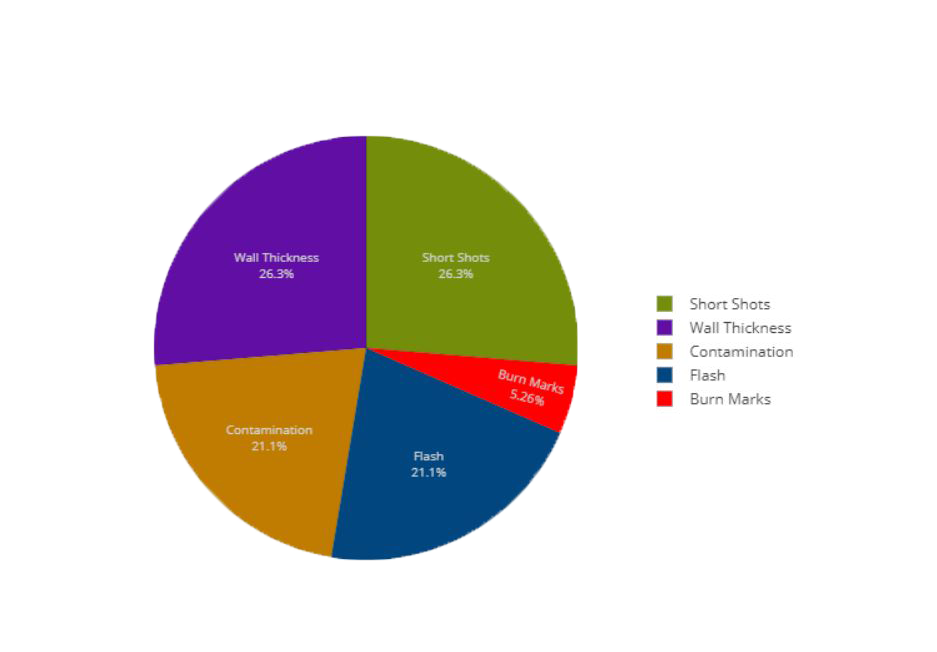
to Enlarge
Defect Collection
Conduct root-cause analysis to improve quality and eliminate warranty costs so you can reduce product recalls, revenue loss, decrease in customers, and damage to your brand. PlantStar prioritizes defects and charts them out in real time so you can immediately view all your defects for any running job or specific shift. Additional features include unlimited user configurable defect reasons, repair or scrap disposition, and ERP solutions integration.

to Enlarge
Labor Tracking
PlantStar Labor Tracking is designed to collect, report, and forecast labor hours by machine, job, shift, or employee. Labor information is collected and tracked by personnel logging in and out of machines from a DCM or HMI. Employees can be logged onto one or more machines at the same time depending on the category work being done. For this reason, PlantStar Labor Tracking is not typically used as a time and attendance system. It will provide a window to where and how labor is used on the shop floor. It can also report time spent by support personnel at a machine. As a job history is developed the job history labor reports can be used to forecast staffing requirements on a shift or weekly basis. The Labor Tracking feature provides the ability for Operators to log their actions using Process Journal entries, providing an audit trail for activity within the PlantStar MES system. All of this data is stored in a secure database within the PlantStar APU server. This data can then be used for various management information system functions including review, analysis, audit, and reporting, including upstream and downstream integration with ERP systems and functions.
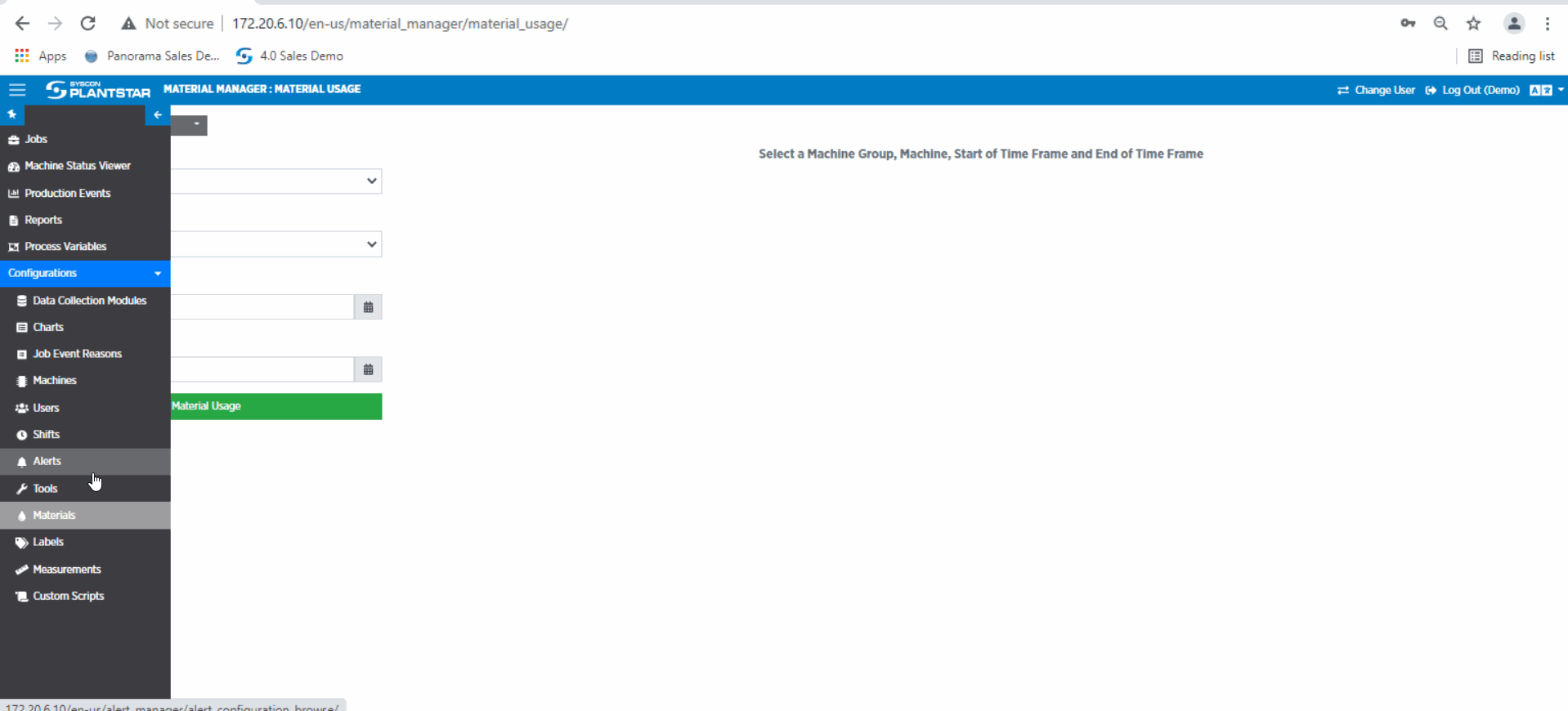
to Enlarge
Material and Tool Tracking
Material Usage Reporting-Generate reports on materials usage by job, shift, day, or other period. Export data back to ERP to improve operations and control.
Material Forecasting-Anticipate material usage/demand based on scheduled jobs and materials specifications.
Material Lot Tracking-Track material lot numbers from ERP work order through production and maintain association between material lots and jobs, work orders, and finished goods to provide traceability and control.
Tool Life Tracking-Tracks the time and number of cycles that an individual tool was used. Includes access to Tool Maintenance where life cycle information can be reviewed and maintenance can be tracked.
Production Monitoring Benefits
Take advantage of integration features, tracking capabilities, and a variety of other functionalities that help streamline your processes and deliver quality products.
Operator Tracking
Labeling and Barcoding
ERP Integration
Voice Output
Remote Monitoring
Real-Time Data
Process Journals
Process Variables
Tools
Tool Maintenance Events
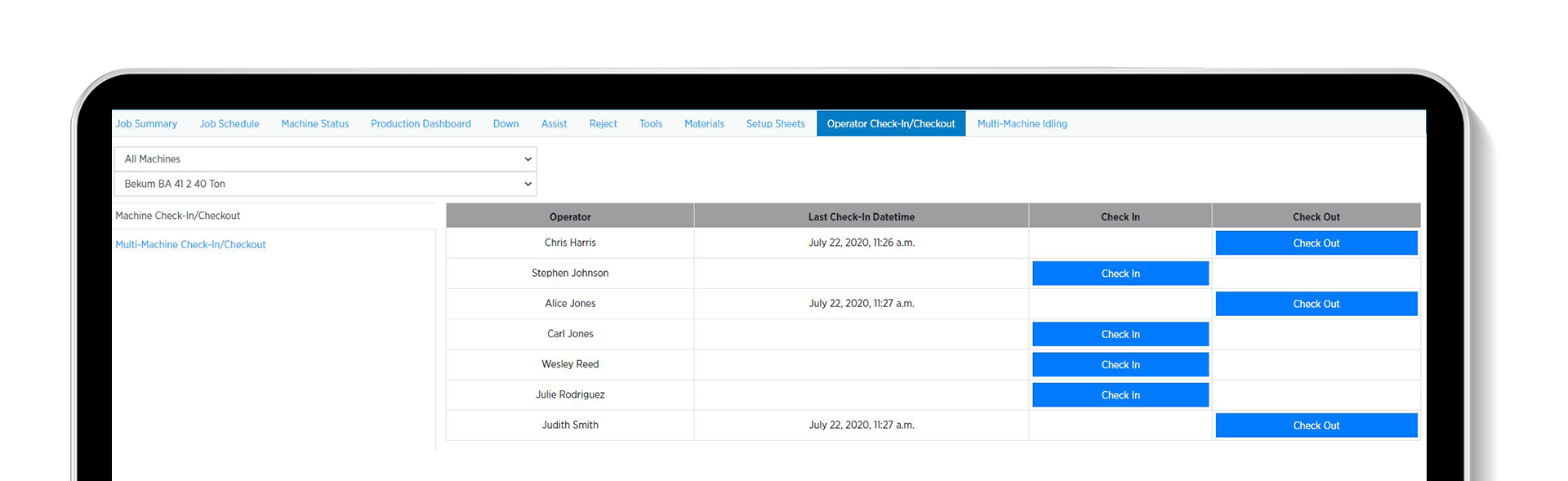
to Enlarge
Operator Tracking
Eliminate the guesswork in associating specific users with completed action events. With PlantStar 4.0 operator tracking, users can quickly identify operator action events using simple track-and-trace capabilities. All operator actions and system configuration changes are logged and can be identified with the associated PlantStar user. User autentication can be assoicated with a user login or badge scan.
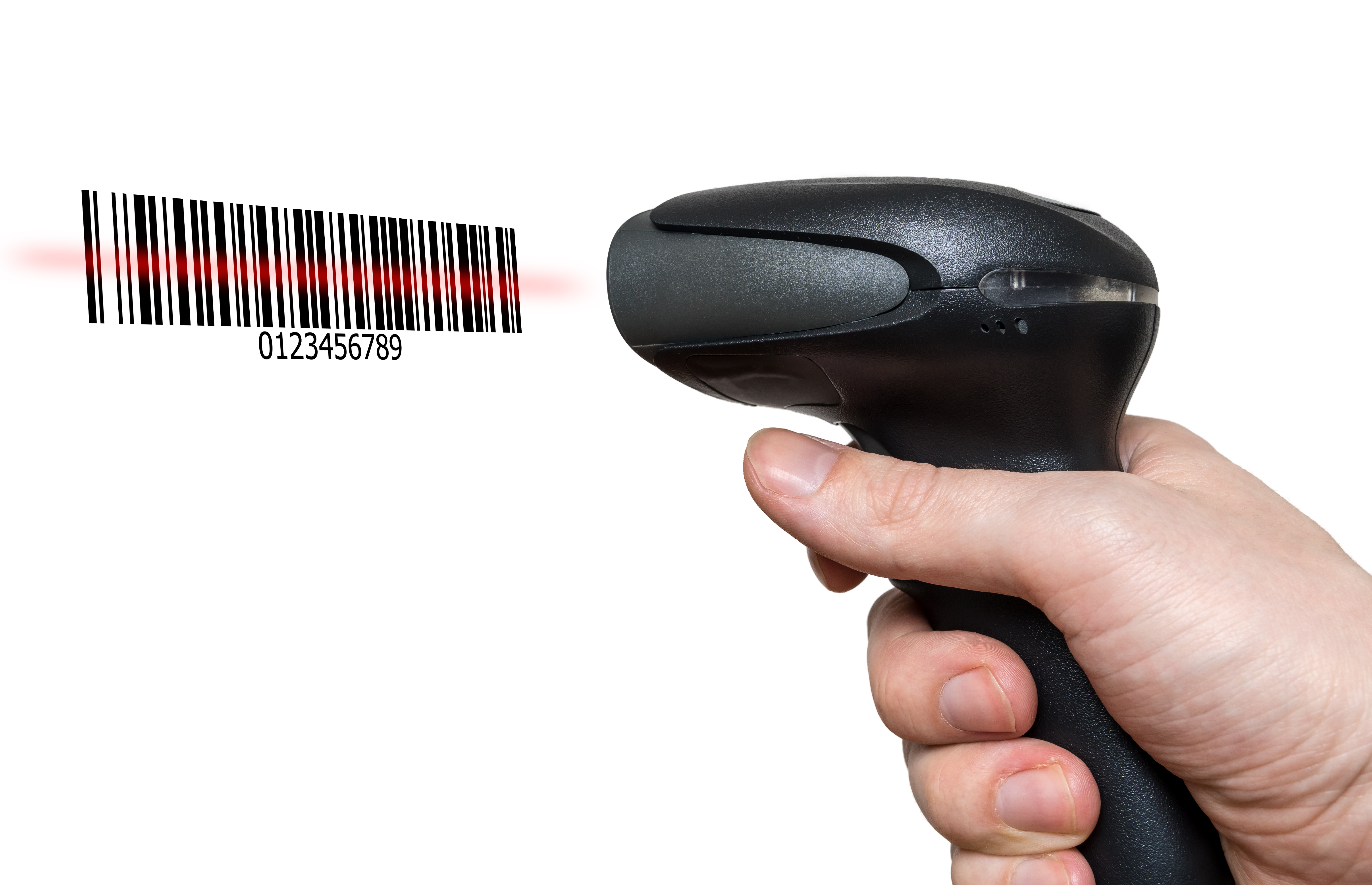
Labeling and Barcoding
Reduce the percentage of recalls due to product label errors with labeling and barcoding capabilities that strengthen compliance, increase productivity, and reduce operating costs while focusing on product traceability.
Common use cases for printing labels for totes, packaging and pallets. Label printers may be connected via network or directly to a PlantStar DCM and barcode or other labels may be printed for any process requirement.
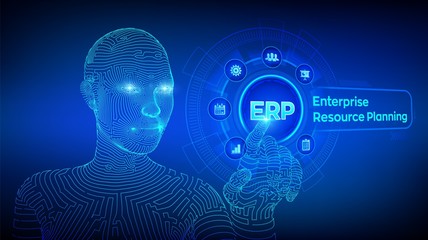
ERP Integration
PlantStar has extended its options for importing and exporting data to ERP systems. We now provide multiple machine specific standards to be imported in any one import file. Our end-of-shift export utility can now notify you of any machines that have failed to report the end-of-shift event. This is usually a sign of network problems between the host and the data collection module. In conjunction with the previous feature, we can export only data for late reporting machines. So once the initial communications problem has been resolved, the data that was missed in the first end-of-shift will be exported. Our export utility can now be set to perform an incremental export. That is, instead of one export per shift, it can now do an export on a set interval. This will allow your ERP system to more accurately reflect the current production status of your shop floor.
Some examples include:
- How much finished goods are available or when they will be available?
- How much raw material was consumed and how much more will be required?
- How much machine and labor time was consumed in making the parts?
- When will the machine be available for the next job?
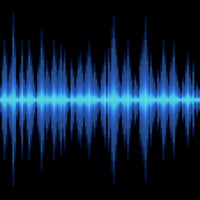
Voice Output
A PlantStar system configured with the Voice Output Option is able to broadcast messages
relating to currently monitored exception conditions such as:
- Down states
- Idle states
- Fast states
- Slow states
- Assist states
- Production exceptions
- Process variable exceptions
- Reject Exceptions
These messages can be heard on speakers or public address systems.
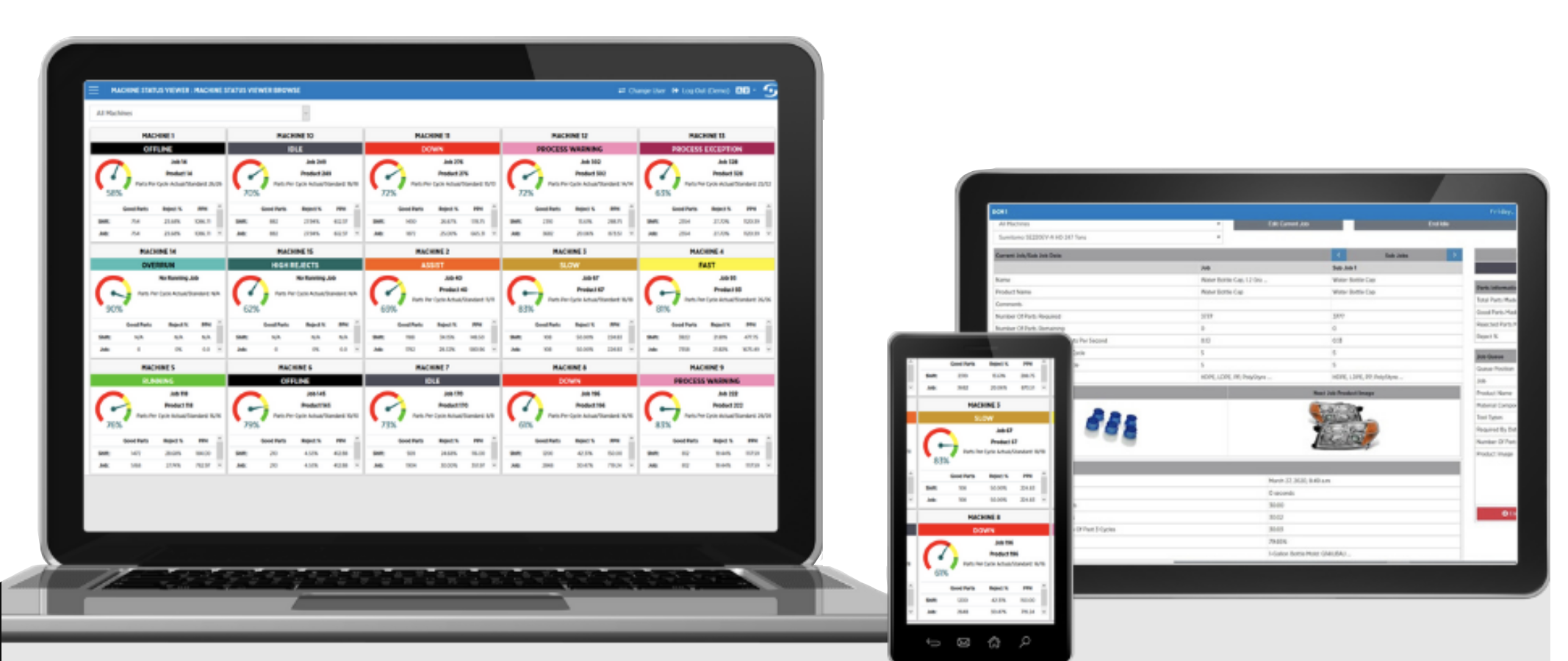
to Enlarge
Remote Monitoring
PlantStar 4.0 is a fully web-based manufacturing execution system. See the status of your production equipment, OEE, parts per hour, reject % etc. wherever you are with remote monitoring functionality from any device connected to the internet.
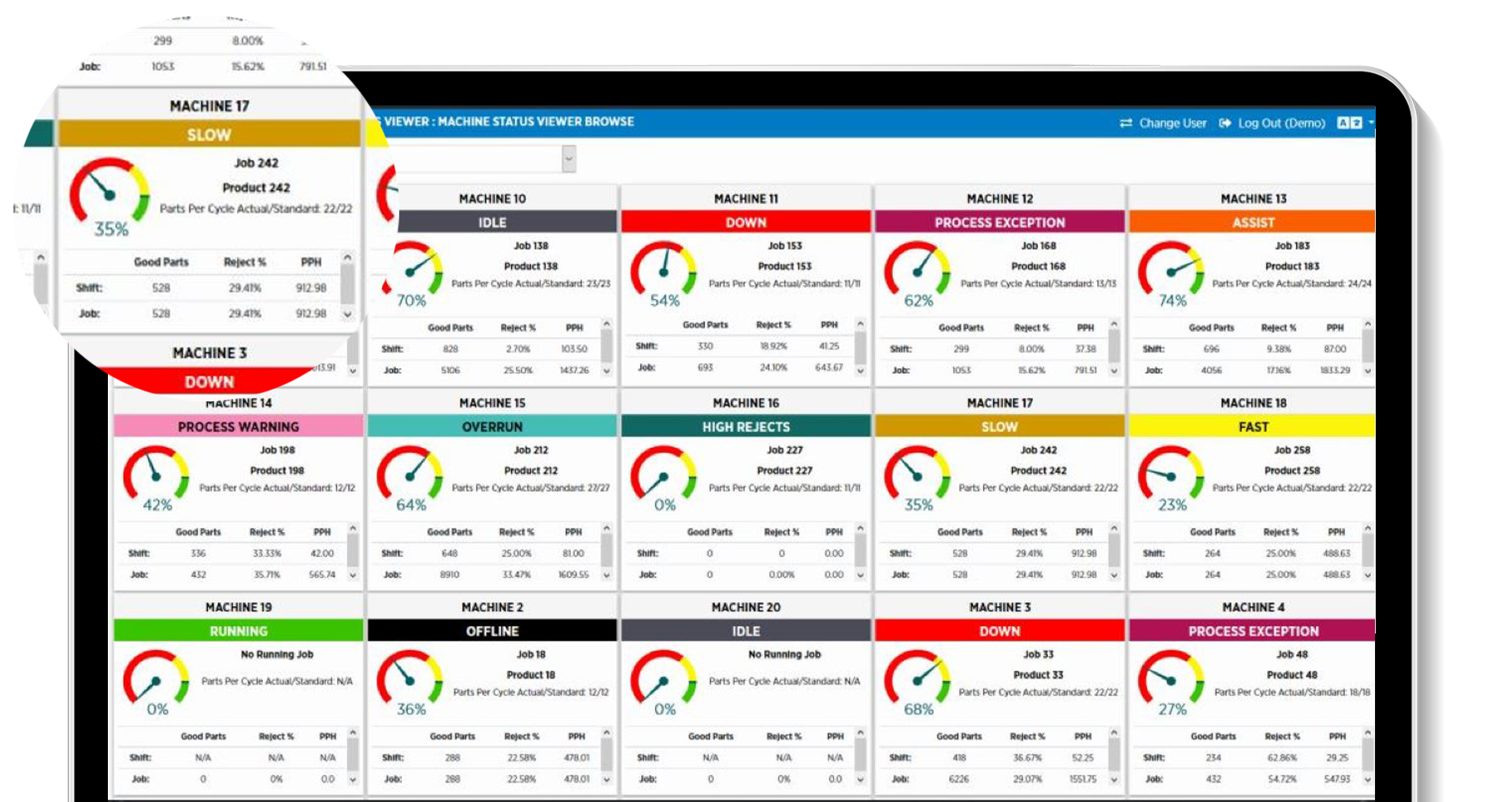
to Enlarge
Real-Time Data
Your machine operators need to be able to access timely data in order to make quick decisions, and PlantStar’s MES provides that and more. Get an up-to-date look at your most important metrics and KPIs on a single, customizable screen. With the Machine Status view, you have insight into the real-time status, efficiency, and production data for any machines you choose. Plus, you can access simplified, color-coded charting with historical and real-time process variable data.

to Enlarge
Process Journals
The PlantStar Process Journal program is a web-based program designed to provide the shop floor personnel with a method to record changes made to a process being monitored by the PlantStar system.
The PlantStar Process Journal system provides an interface for users to record and track equipment maintenance, outages and other problems, as well as the resolutions to those issues. This feature is used in conjunction with our labor tracking option. The data is time-stamped and associated with an individual job, shift and employee. It also has a totally browser-based user interface. So anyone on your network will be able to view the data.
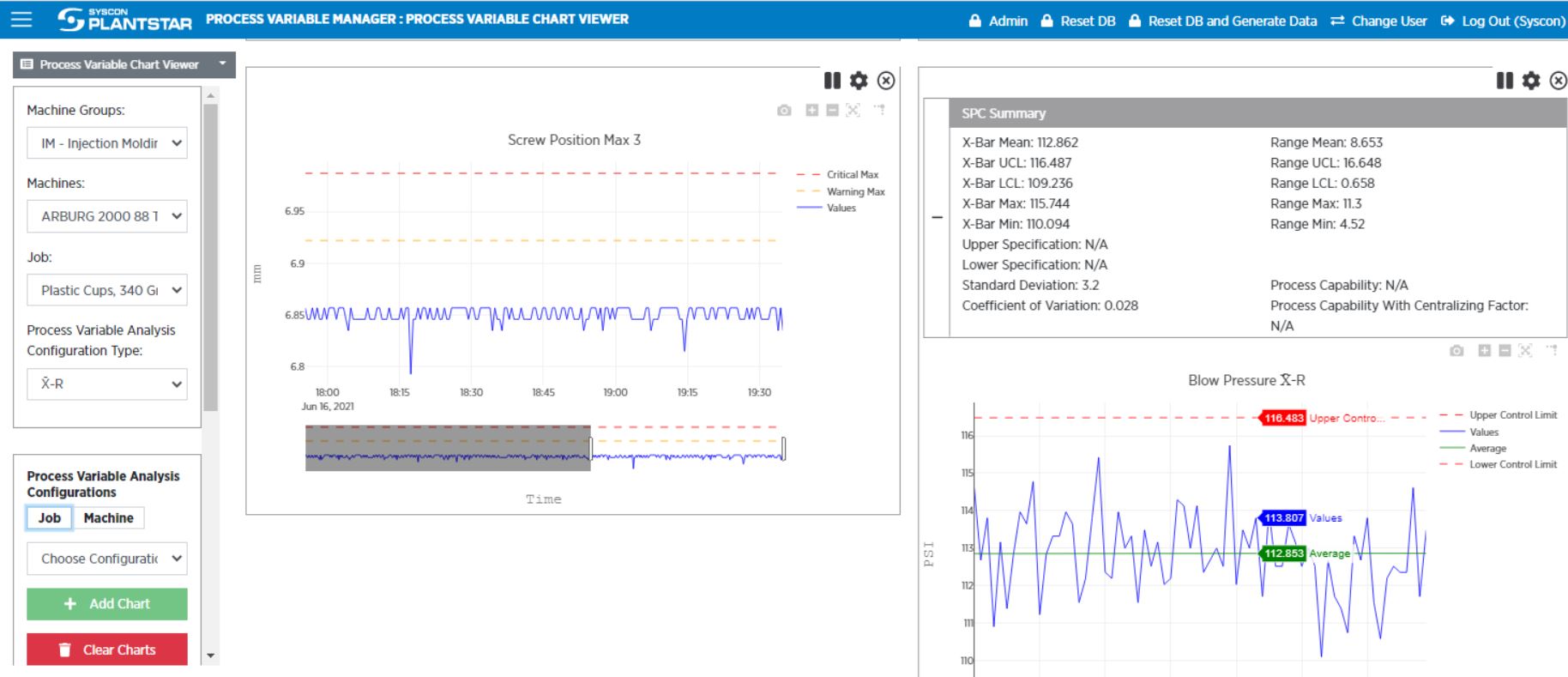
to Enlarge
Process Variables
Types of process variables are used to monitor characteristics which are repeated with every machine cycle. Some of the most common examples of process variables that are monitored through our system are:
Process Variable | Units |
Cycle Time | sec. |
Fill Time | sec. |
Charge Time | sec. |
Hold Time | sec. |
Cooling Time | sec. |
Take-out Time | sec. |
Injection Start Position | in |
Switch-over Position | in |
Cushion Position | in |
Maximum Inj. Pressure | PSI |
Switch-over Pressure | PSI |
Screw Speed | rpm |
Feed Throat Temp. | deg F |
Barrel Zone 1 Temp. | deg F |
Barrel Zone 2 Temp. | deg F |
Barrel Zone 3 Temp. | deg F |
Barrel Zone 4 Temp. | deg F |
Nozzle Temp | deg F |
Themolator 1 Supply Temp. | deg F |
Themolator 2 Supply Temp. | deg F |
Chiller Return Temp. | deg F |
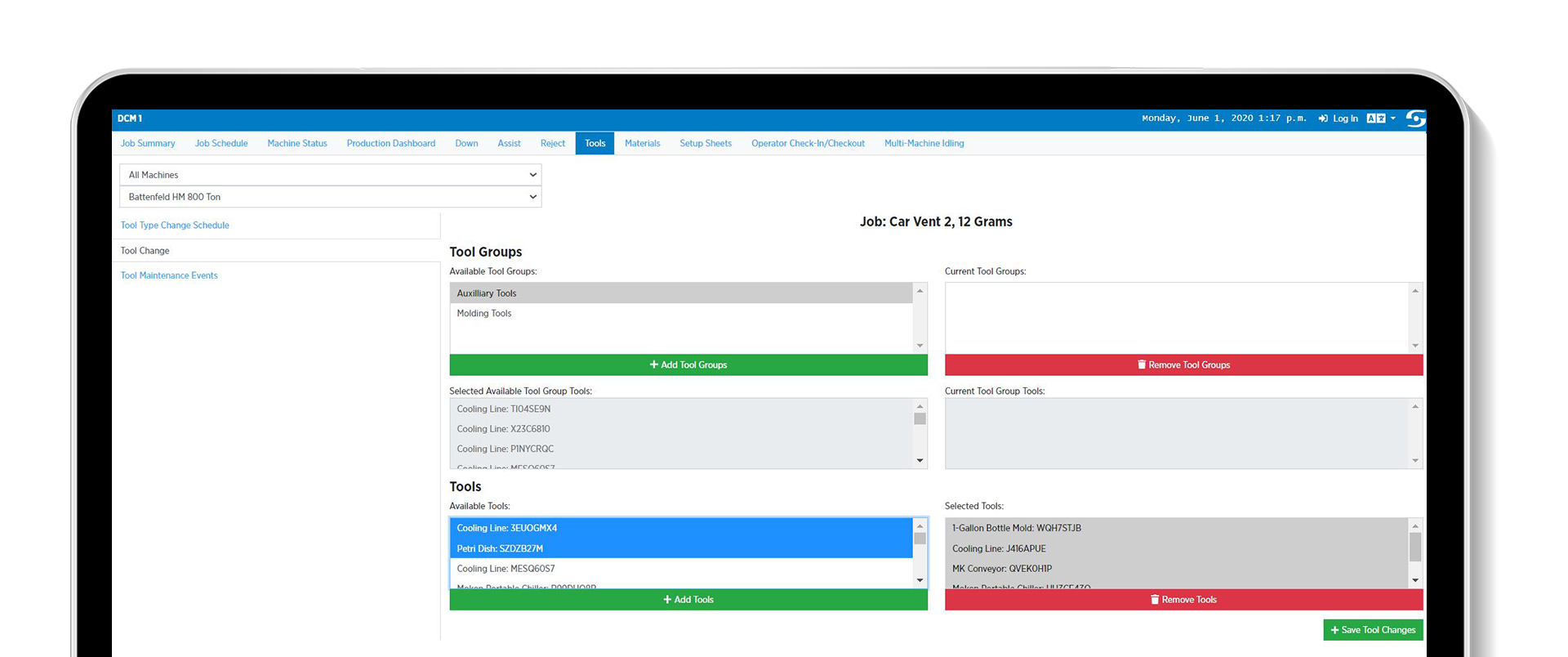
to Enlarge
Tools
A Tool in the system is something physical and unique, and has an associated serial number. Even if there is a similar tool, it is not physically the same tool. A Tool has information tracked. For example, time since it was first pulled out of a box (lifetime), time that it was ran on all the machines (runtime), and the number of cycles that it has been through. Having a similar Tool is what we call Tool Type. You may have 3 tools that are all of the same nature and can be swapped out interchangeably. These 3 tools would all use the same Tool Type.
A Tool Type Group is a group of Tool Types, that is used on a job before it starts running because in many cases you don't know which Tool of a particular Type you want to use until the job actually starts. When you start the Job you can select which Tool will be used and the system will present you with the available options based on the Tool Type Group Selected.
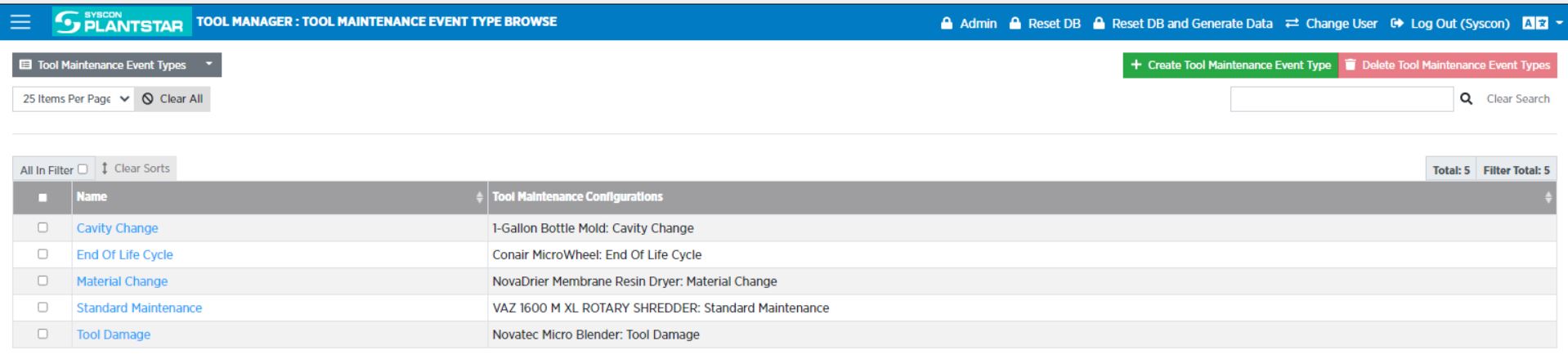
to Enlarge
Tool Maintenance Events
Tool Maintenance is part of the Tool Life Tracking package. Tool Life Tracking as a whole is meant to help cover your (TPM) Total Productive Maintenance needs. Tracking of individual tools and their respective usage including operation time, time since it was initially put into commission, and number of cycles that it has been through. The Tool Maintenance aspect of this is meant as a way to log these tool maintenance events, which will include the tool, job that was running when the maintenance occurred if any, type of maintenance, event datetime, duration, and comments. You can create the different kinds of maintenances and their necessary frequency.
Process Monitoring Features
Process Monitoring measures the process variables at the time of manufacturing.
Process Monitoring allows process variables to be created and tracked during a job. The data can then be viewed on charts or spreadsheets in real-time. SYSCON PlantStar has decades of experience with machine protocol interfaces and allows for Statistical process control (SPC). SPC is a method of quality control which employs statistical methods to monitor and control a process.
Stay up to date about the process variables that go into your projects, with the ability to easily make adjustments as necessary. If defined for a machine, unlimited process variables can be monitored. Most process variables are collected once per machine cycle. These types of process variables are used to monitor characteristics which are repeated with every machine cycle. Some of the most common examples are pressure, temperature or time duration process variables. When it comes to process monitoring PlantStar's manufacturing execution system is unmatched.
Physical or Machine Interface
Process Single Value
Process Profile
Process X Bar-R with Chart Overlay
Process Variable Table Viewer
Tailor Process Variable Limits
Process Variable Chart Viewer
Process Trend SPC
Process Variables Injection Molding
Process Variables Blow Molding
Process Variables Extrusion Blow Molding
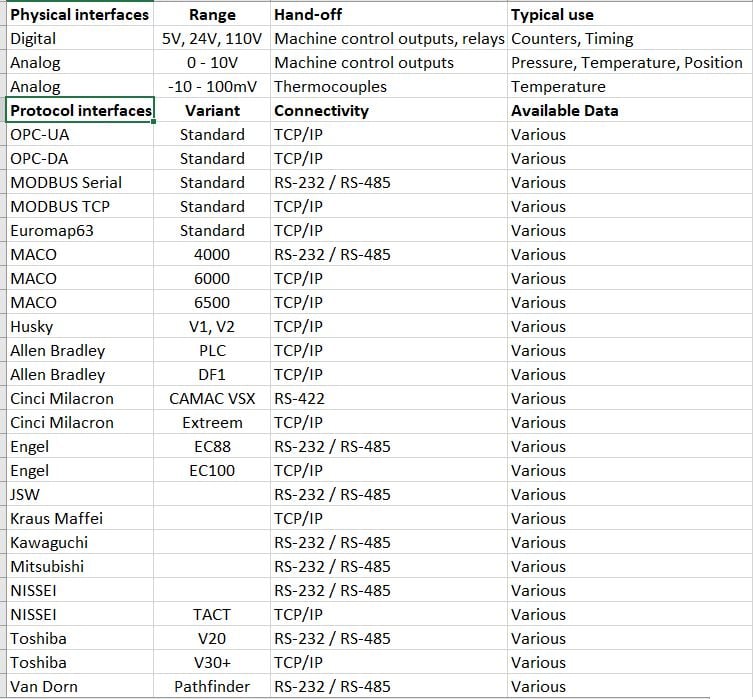
to Enlarge
Physical or Machine Interface
Some MES systems limit the user on the number of process variables, but with PlantStar you can input an UNLIMITED number of process variables and process variable profiles.
Measure specific time, temperature and pressure process variables and receive instant alerts when they go out of tolerance. PlantStar has the ability utilize PHYSICAL or a plethora of machine protocol interfaces. The image displayed shows common machine interfaces.
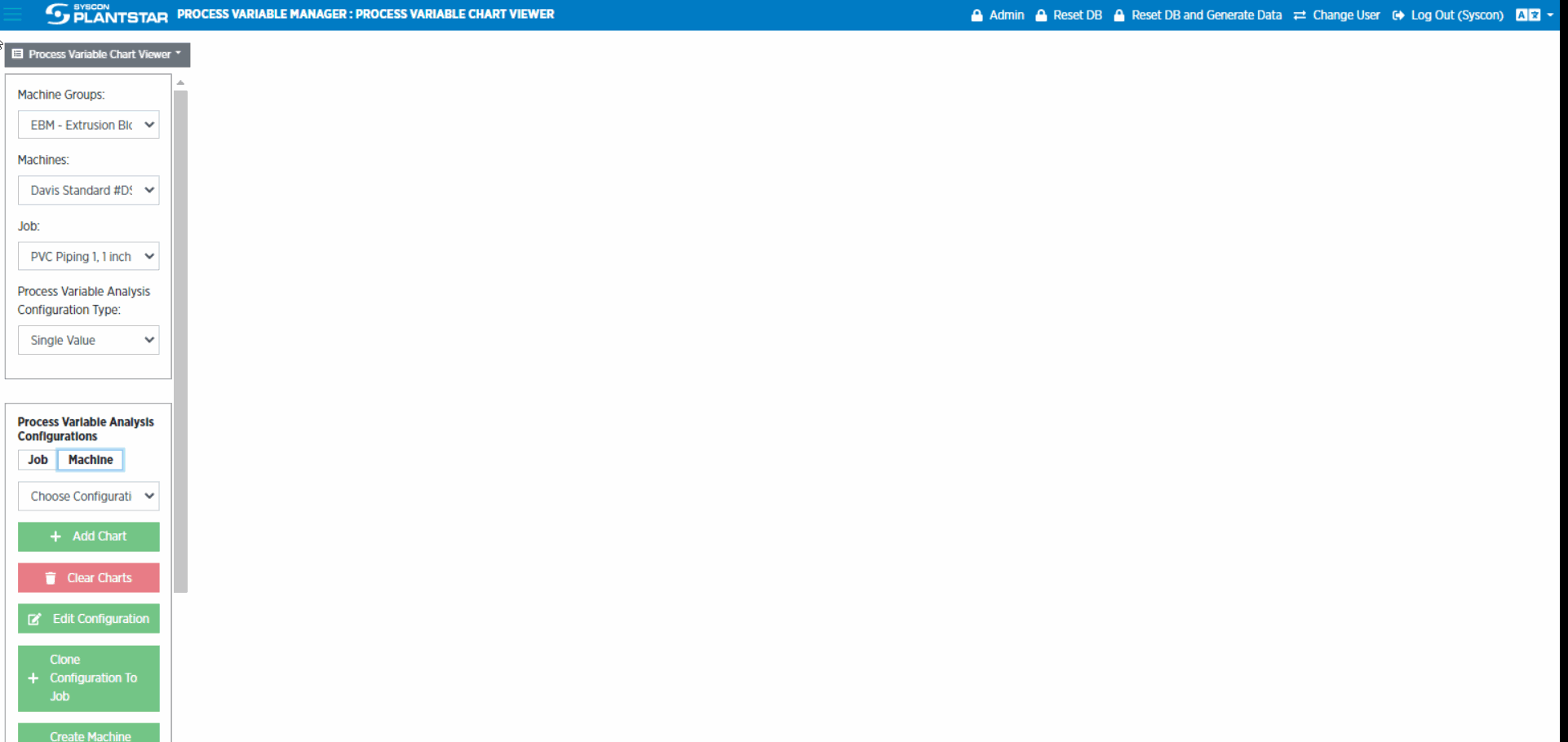
to Enlarge
Process Single Value
1 value for every cycle. Ability to plot that value for each cycle. This is very helpful to look at process trends
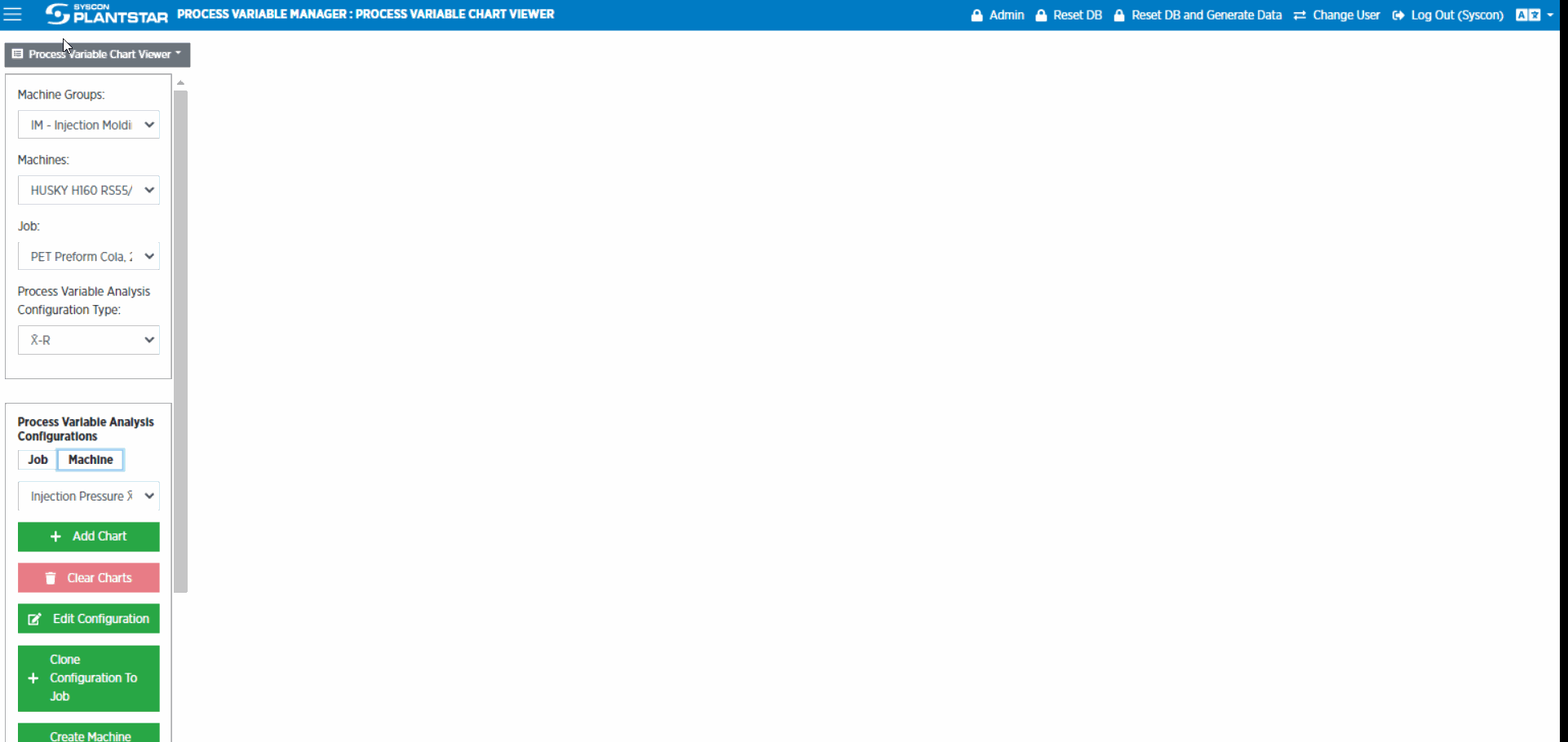
to Enlarge
Process Profile
The process profile shows a single cycle and all of the changes over time within that cycle.
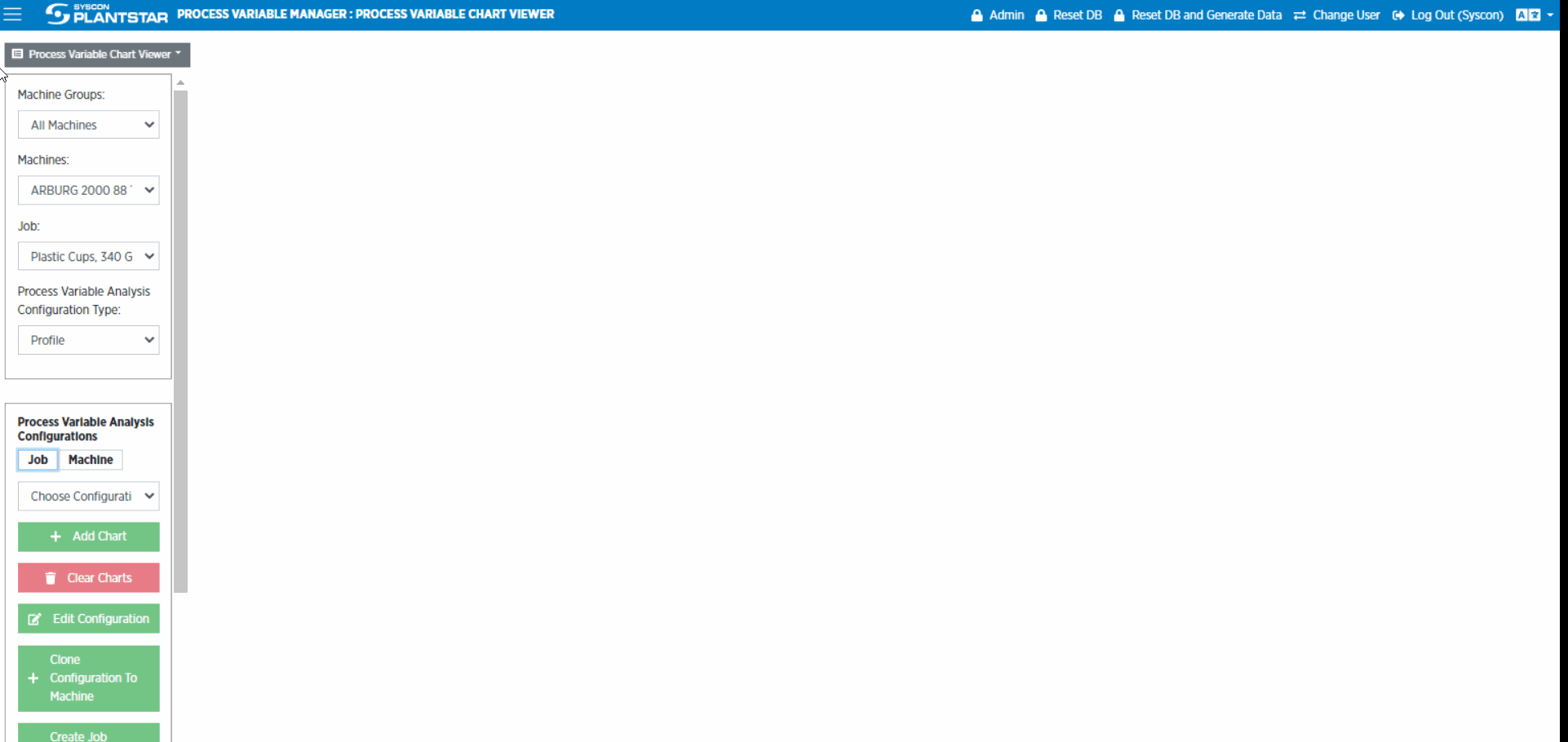
to Enlarge
Process X Bar-R with Chart Overlay
SPC Chart. How your process trends are doing over a longer period of time
The x-bar and R-chart are quality control charts used to monitor the mean and variation of a process based on samples taken in a given time. The control limits on both charts are used to monitor the mean and variation of the process going forward. If a point is out of the control limits, it indicates that the mean or variation of the process is out-of-control. PlantStar also has the ability to add Process Overlay Charting which allows you to overlay a various amount of different process variables.
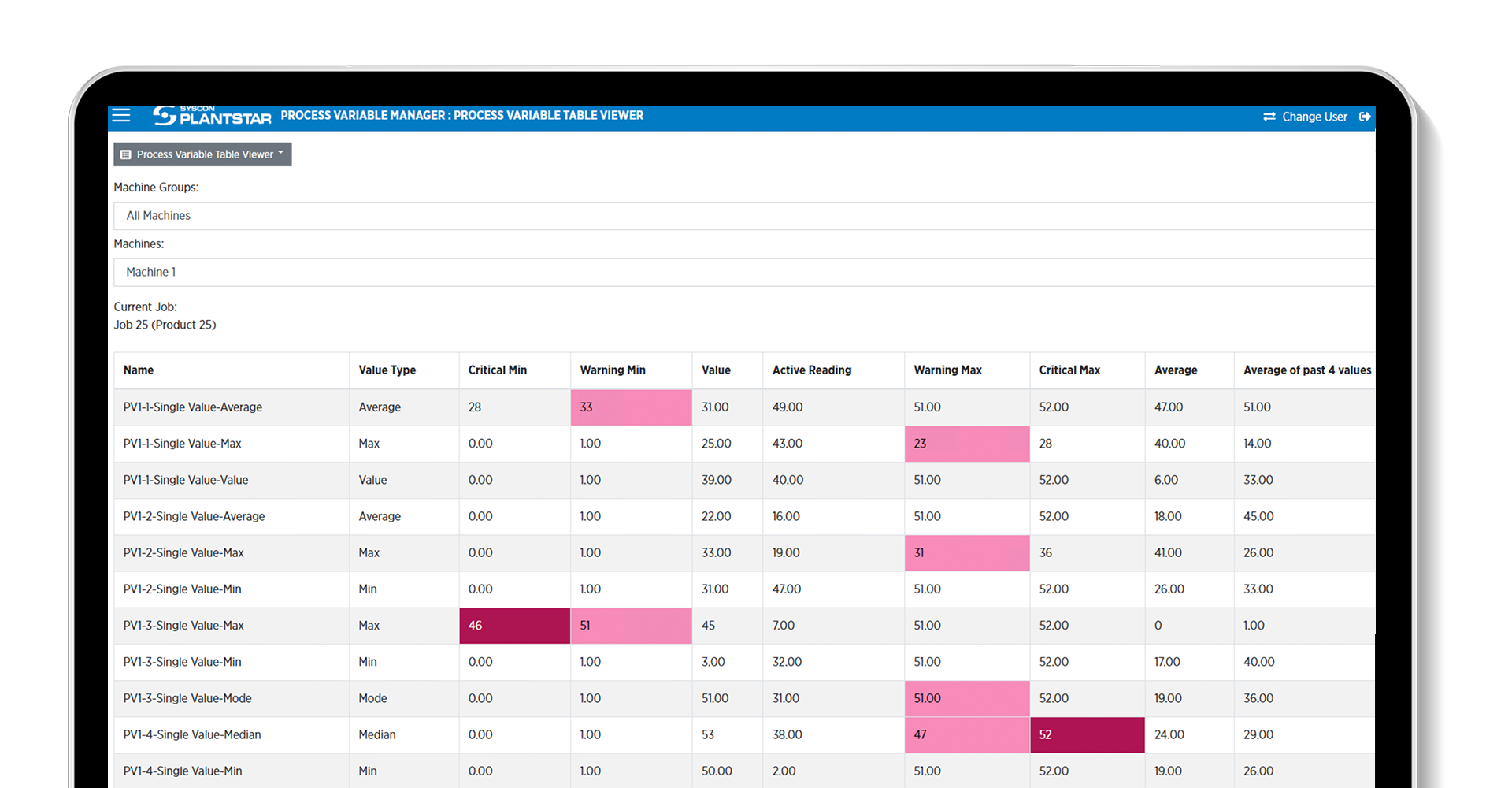
to Enlarge
Process Variable Table Viewer
Stay up to date about the process variables that go into your projects, with the ability to easily make adjustments as necessary. If defined for a machine, unlimited process variables can be monitored. Most process variables are collected once per machine cycle. These types of process variables are used to monitor characteristics which are repeated with every machine cycle.
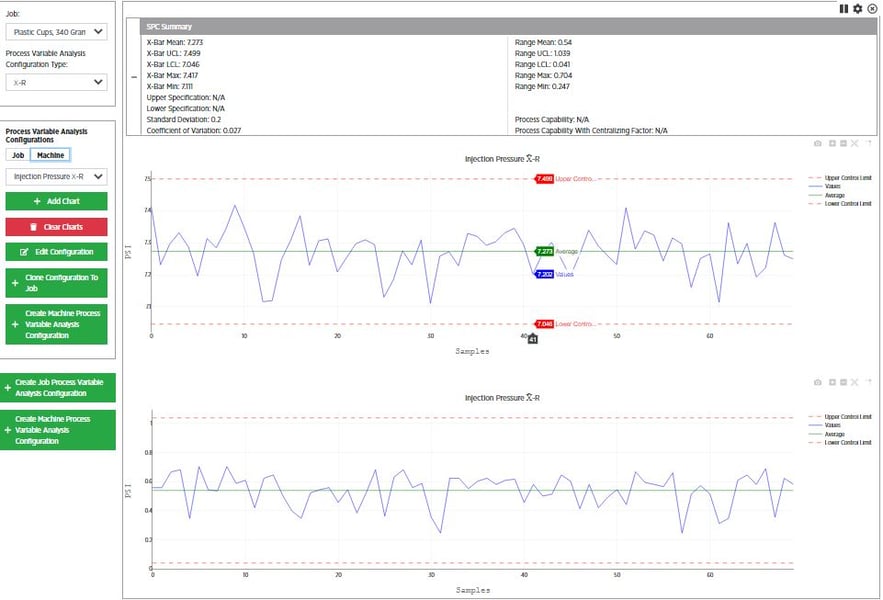
to Enlarge
Tailor Process Variable Limits
Use PlantStar to set upper and lower limits to your process variables and easily adjust as production needs change.
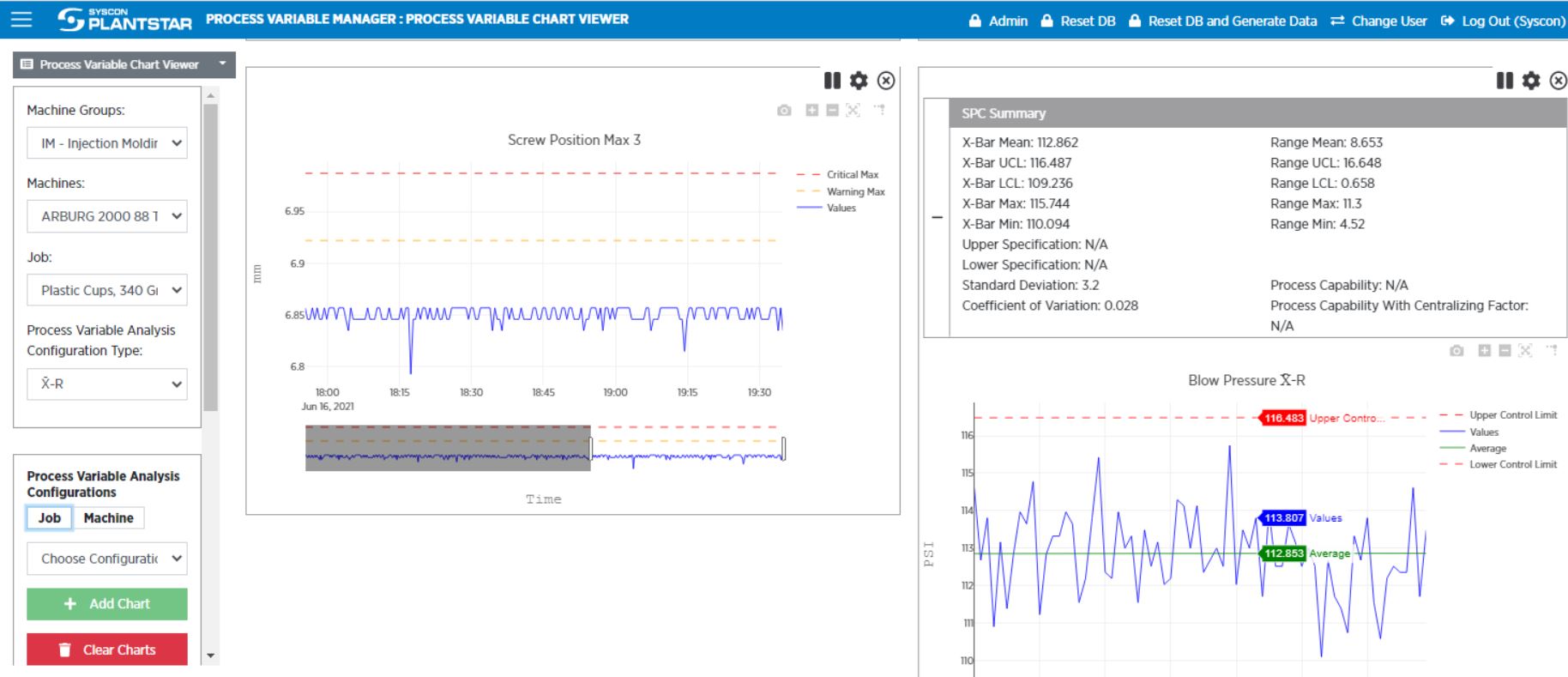
to Enlarge
Process Variable Chart Viewer
View live readings of KPIs including pressure, temperature, injection position and much more in real time. Tweak the chart configuration on the fly for a truly granular view into the health of your machines.
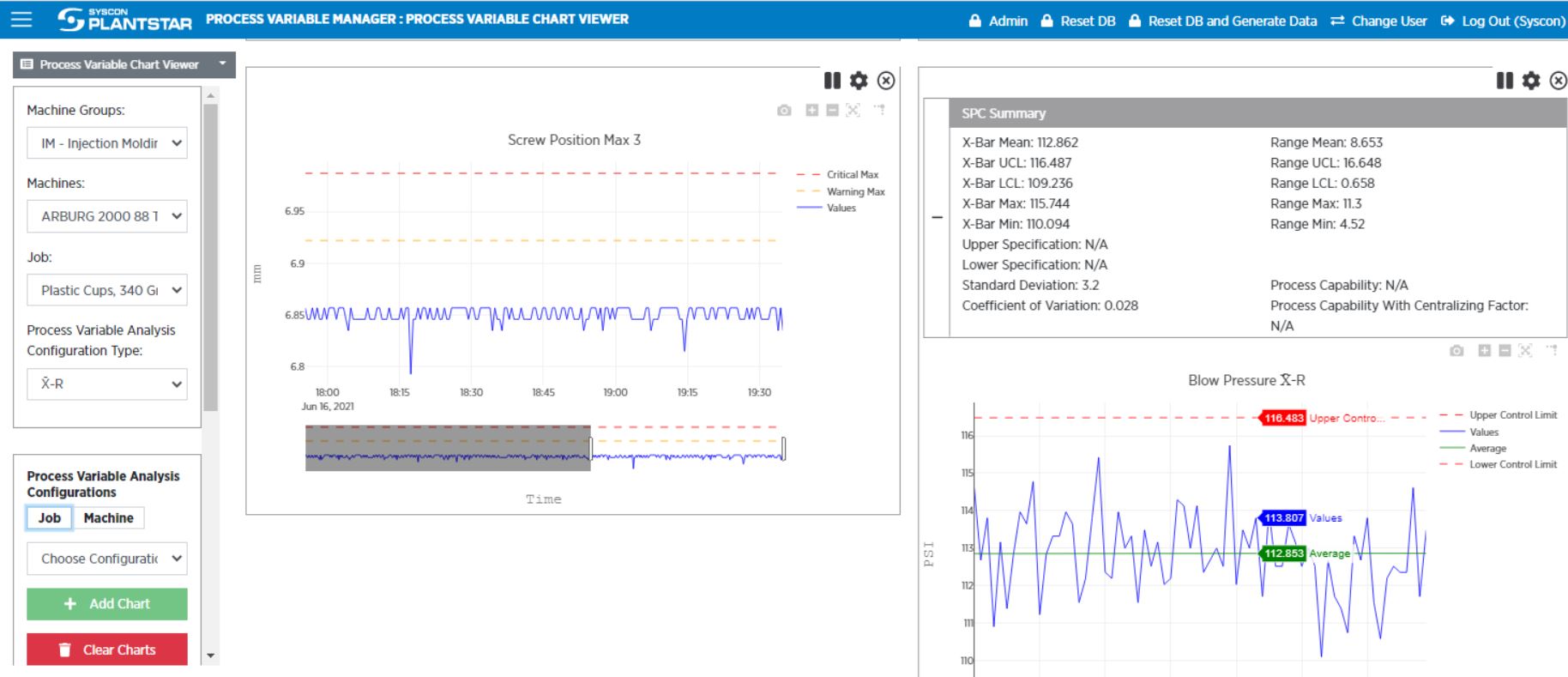
to Enlarge
Process Trend SPC
This technique involves creating a control chart that shows the upper and lower warning and action limits based on a target value for your parameter. Using the control chart, you can look for deviations from a normal process behavior and the PlantStar system will immediately send alerts.
Stay up to date about the process variables that go into your projects, with the ability to easily make adjustments as necessary. If defined for a machine, unlimited process variables can be monitored.
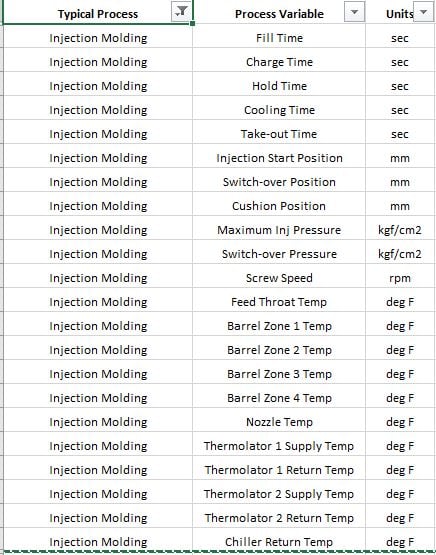
to Enlarge
Process Variables Injection Molding
The image that is displayed are common process variables that our customers measure for injection molding.
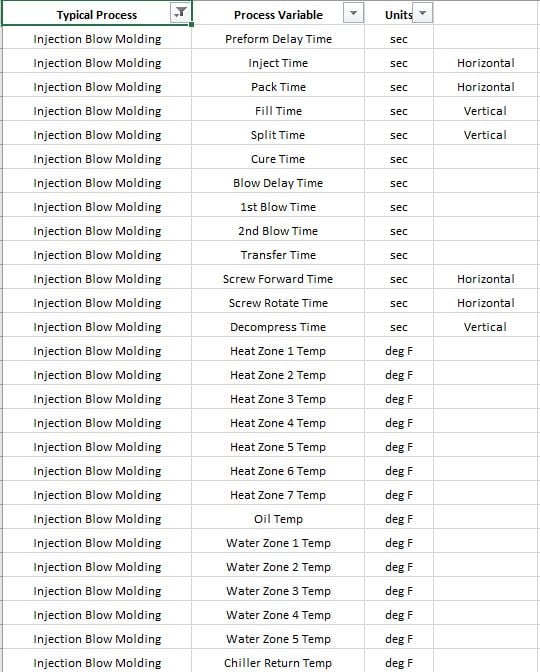
to Enlarge
Process Variables Blow Molding
The image that is displayed are common process variables that our customers measure for injection blow molding.
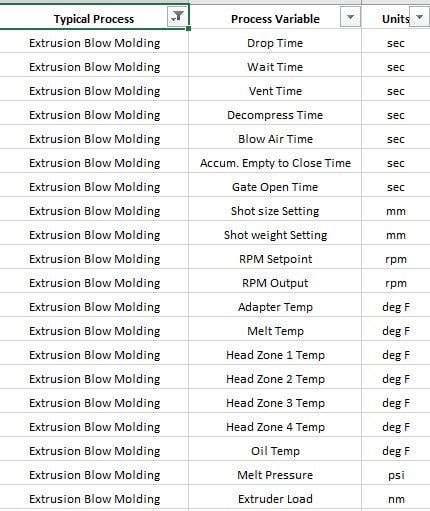
to Enlarge
Process Variables Extrusion Blow Molding
The image that is displayed are common process variables that our customers measure for Extrusion Blow Molding
See The Benefits of Robust MES Software
Could your manufacturing operation benefit from more data? With a robust Manufacturing Execution System (MES), you can combine Production & Process Monitoring to improve productivity and ensure quality and efficiency.
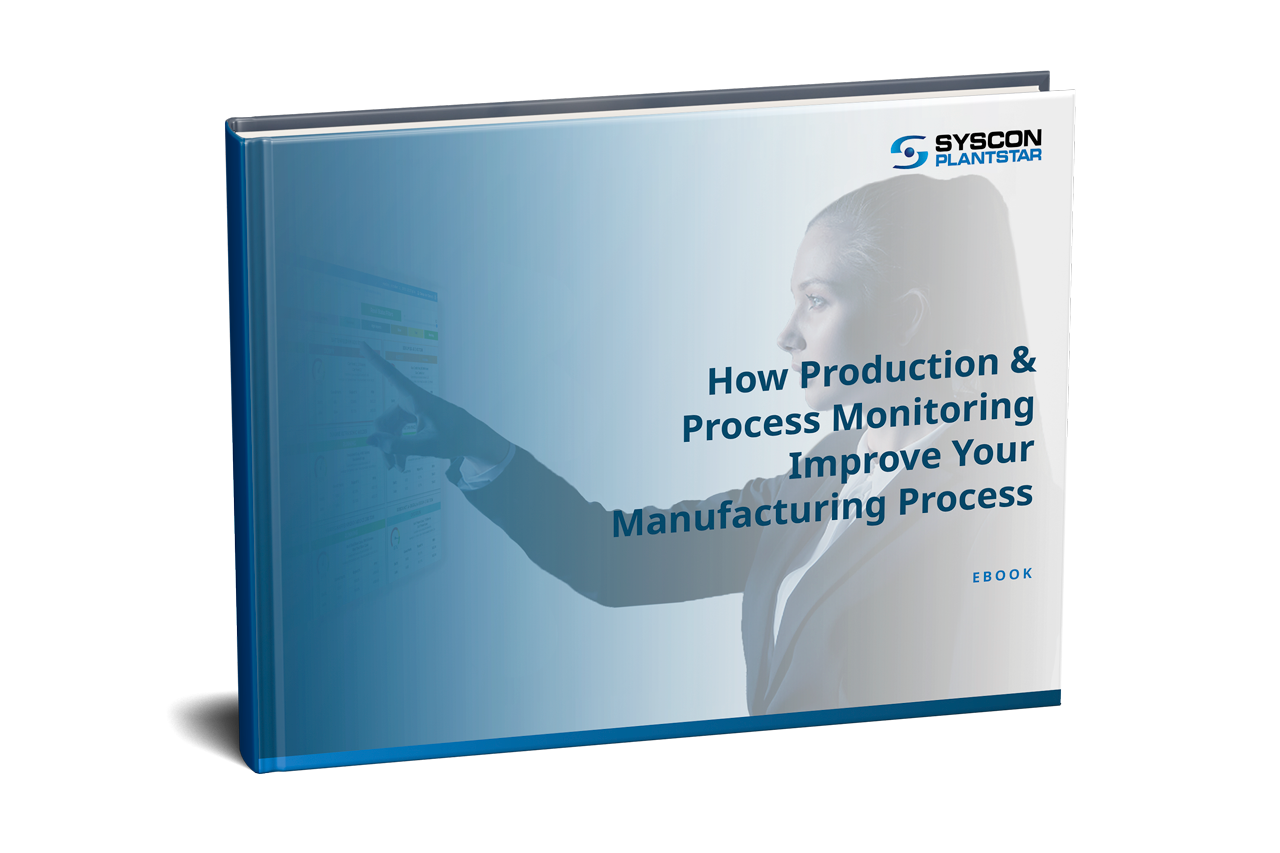
What Our Customers Say
We chose SYSCON PlantStar to be our MES system as it provided us with a wealth of production and process information, including scheduling, product specification, OEE data, labor and process tracking in a flexible, friendly and real time environment that assist us in achieving our operational excellence goals. Over the years (20+ years) PlantStar had validated that we made the right decision by providing us with great customer service and support coupled with leading edge technology. I would highly recommend their services to any other company that is in the market for MES system
With PlantStar, we’ve reduced our internal and external corrective action reports by 92.8%, with major gains in first-time quality improvements and customer satisfaction. An initial savings of $400,000 was realized within five months of implementation.
PlantStar has proved vital to our Manufacturing efficiency and has introduced the ability to stay connected remotely to make key real-time decisions. It has changed the way we operate!
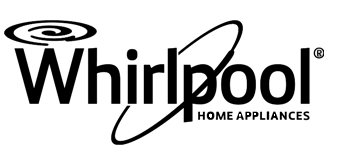
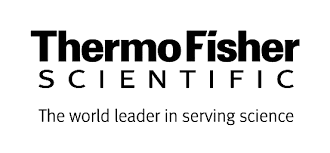
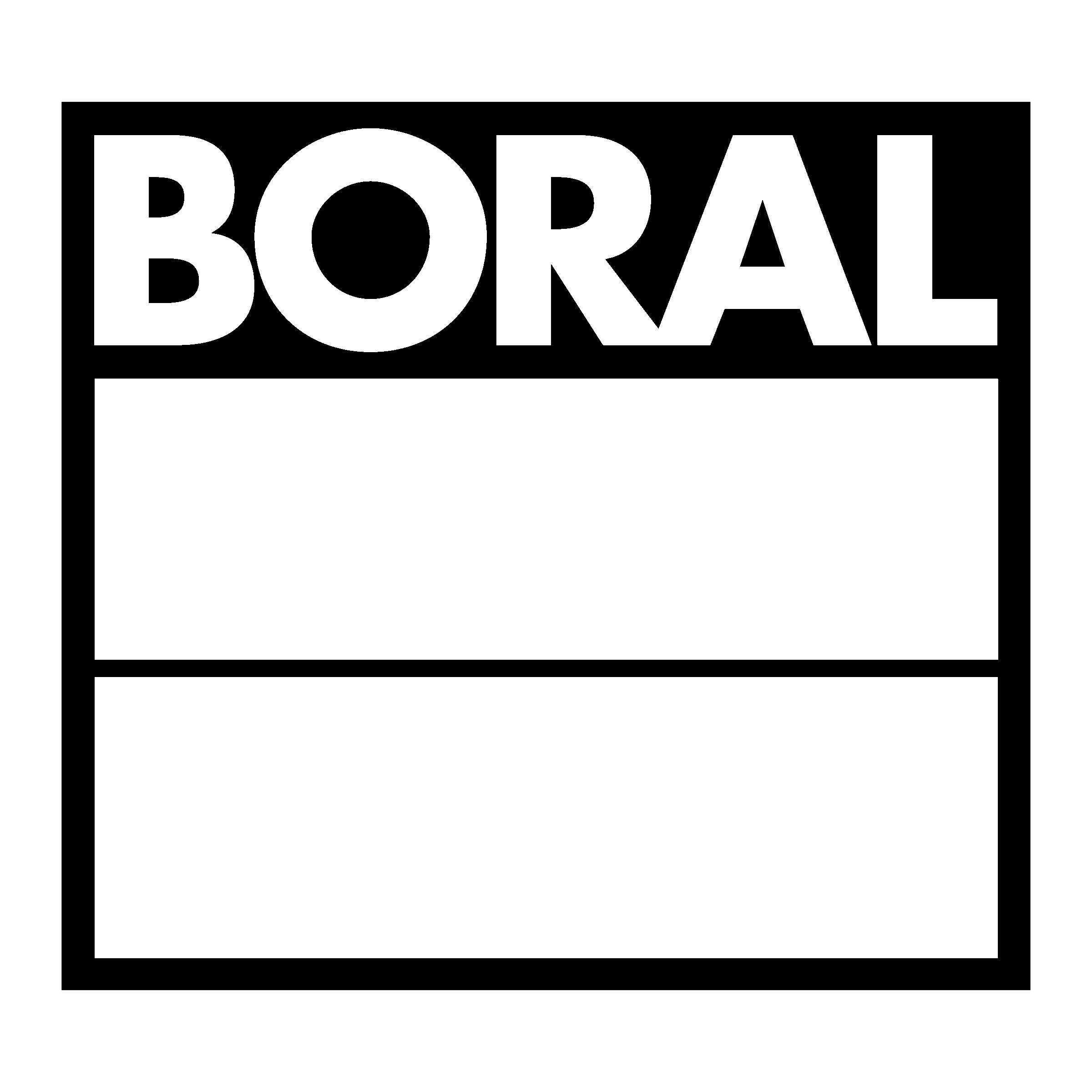
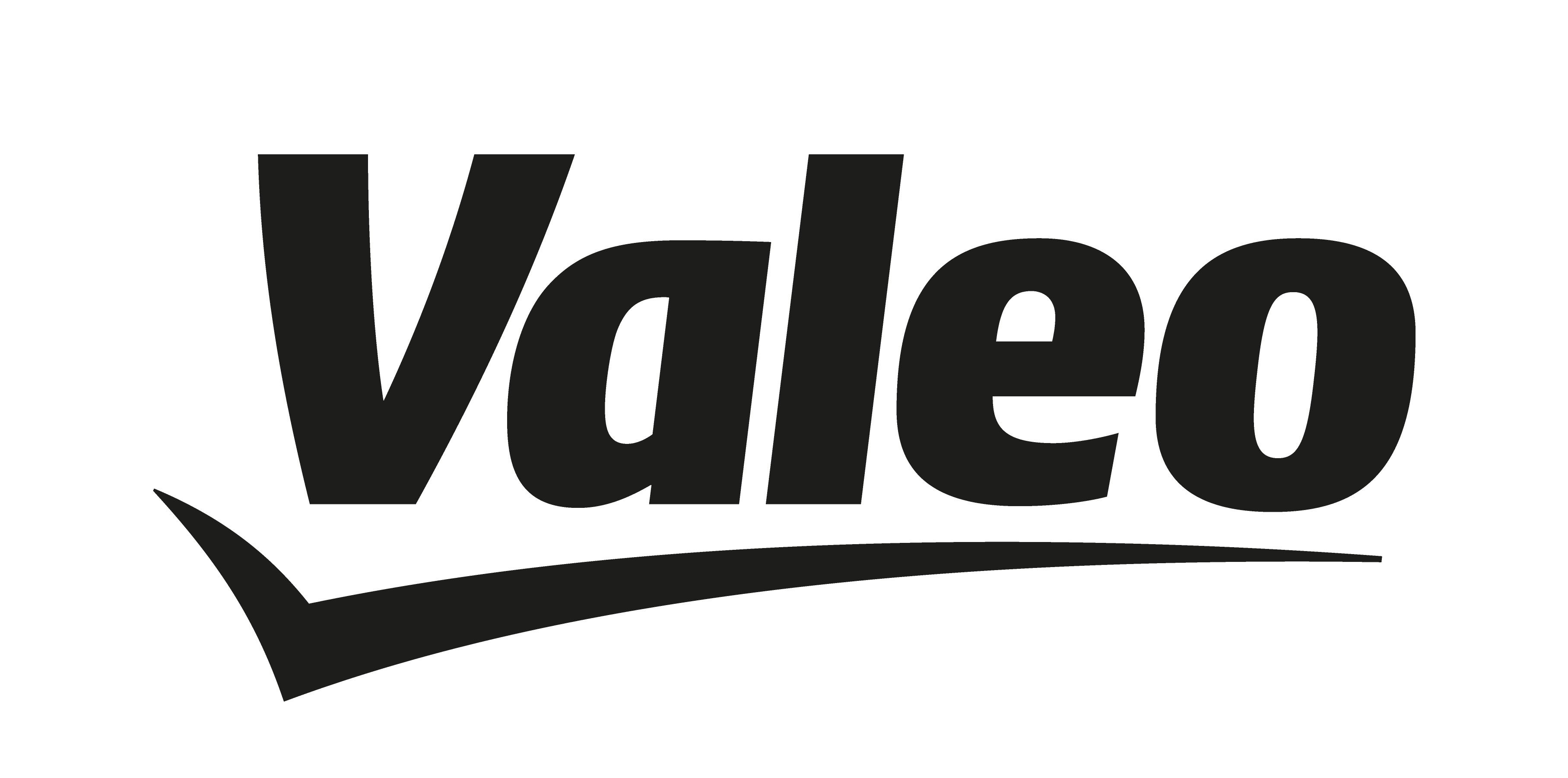
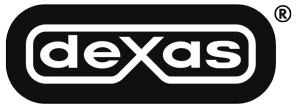
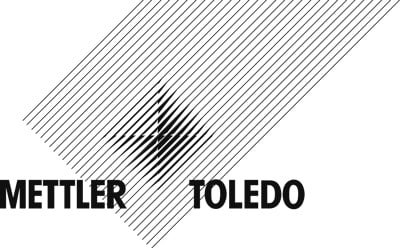


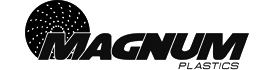
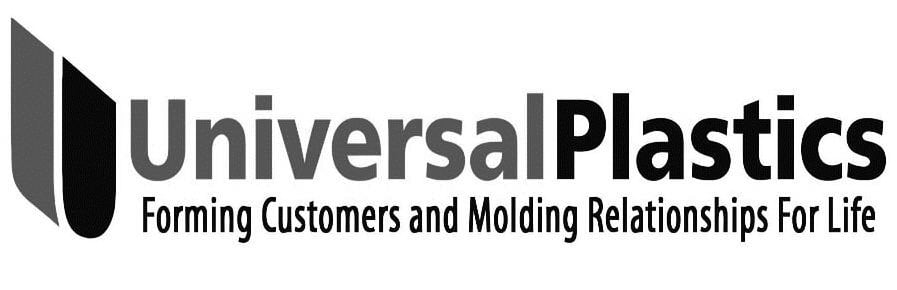
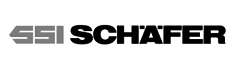
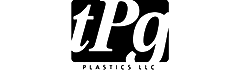
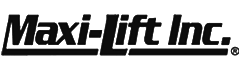
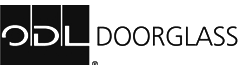
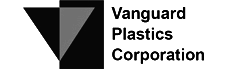
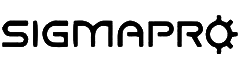
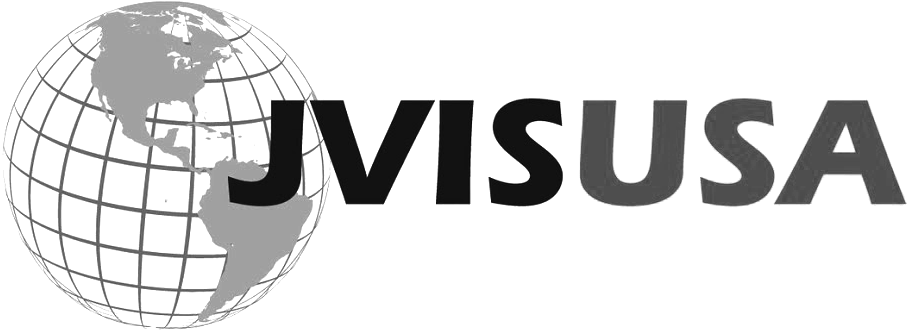
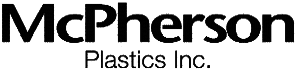
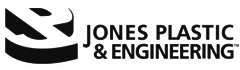
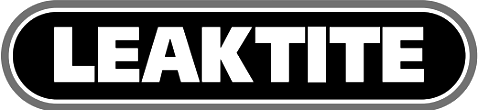
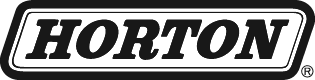
.png)
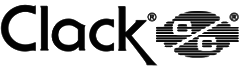
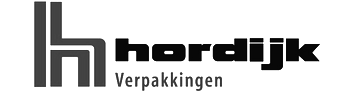
Want a firsthand look at how PlantStar works?
Contact us today to schedule a demo!